Understanding Thermography
Thermography is a key predictive tool It allows us to visualize heat patterns invisibly. This non-invasive method creates visual temperature maps using infrared radiation. It was originally developed in the 1950s.
I first used thermography at a car factory. We detected overheating parts on production lines. It was eye-opening that we could now spot issues before they became major problems.
The Science Behind Thermal Imaging
Thermography centers on infrared radiation. All objects above absolute zero emit this energy. Thermal cameras capture and convert this invisible radiation into visible images.
The underlying physics fascinates me. Heat moves through conduction, convection, and radiation. Thermography focuses on radiation, part of the electromagnetic spectrum just beyond visible light.
In my consulting work, I’ve found that grasping these concepts is essential. Proper data interpretation requires more than just aiming a camera at hot areas.
Thermography in Building Assessment
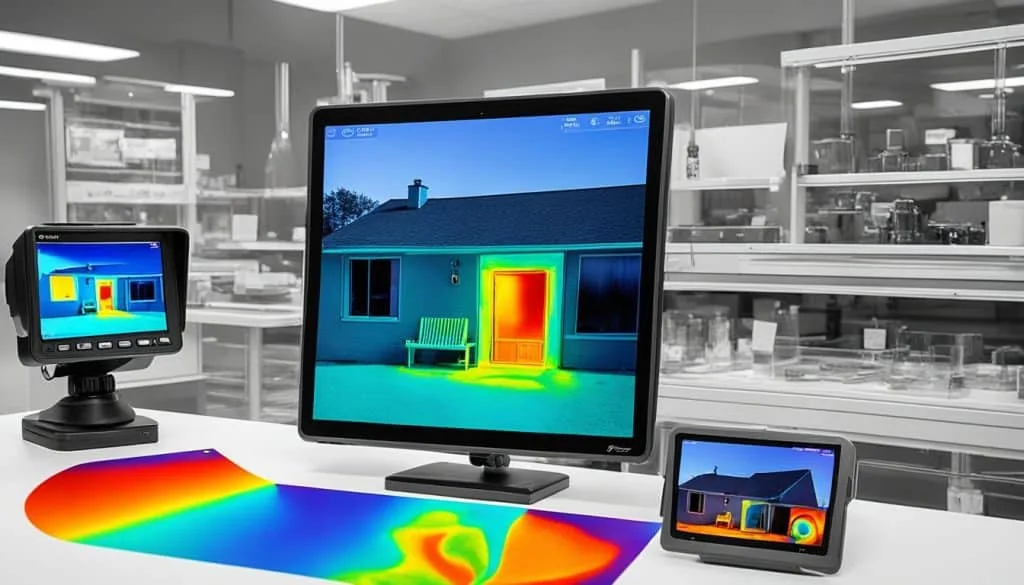
Thermal imaging has changed how we evaluate structures. It’s like a building health check. for efficiency. We use it to identify insulation gaps, detect hidden moisture, and assess energy efficiency.
A client once approached me about their energy-intensive office building. Using thermal imaging, we found significant heat loss around windows and doors. These simple fixes reduced energy costs by 20%.
The benefits extend beyond cost savings. Thermography helps prevent potential issues. For example, water leaks appears clearly in thermal images before visible damage occurs.
Electrical Systems and Thermal Imaging
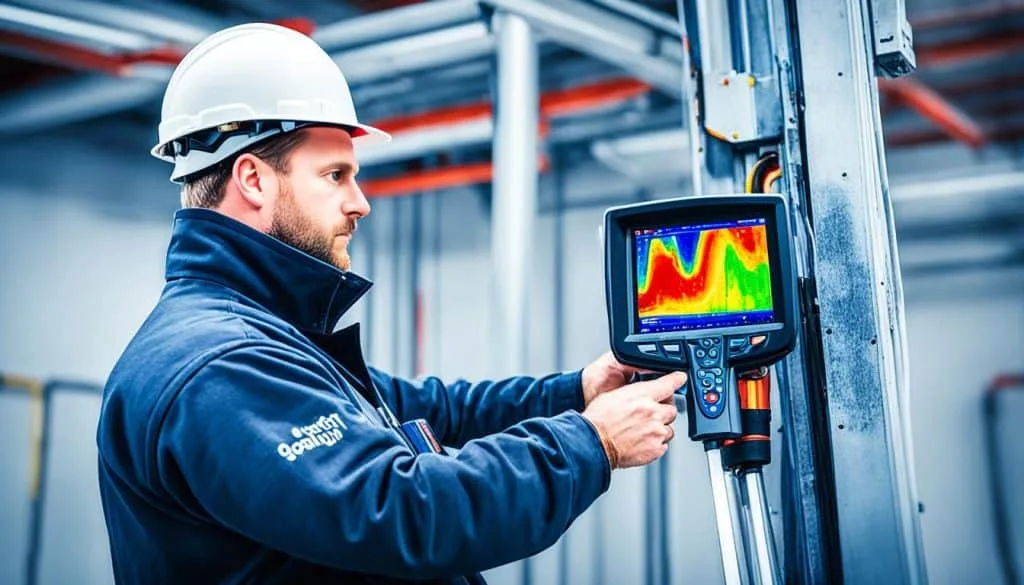
In electrical systems, heat outside the manufactures recommended specification often indicates problems. Thermal imaging serves as an early detection system. It identifies overheating components, loose connections and unbalanced loads.
It also has potential to prevent fires and saved lives. I remember on instances ,were we discovered a dangerously overheating circuit breaker. It posed a serious risk, and was undetectable by the naked eye. The potential risk to the business
Several company’s I have worked with have it as a built in requirement as part of there insurance policy to carryout Thermography.
Thermography in Mechanical Systems
Mechanical systems are well-suited for thermal imaging. Friction creates heat, and excessive heat often signals increased wear. We look at bearings, gears, and other moving parts when creating a route for mechanical thermal checks .
It’s particularly useful for HVAC systems. I’ve used it to locate inefficient ductwork, insulation leaks, and faulty components. After optimizing based on thermal scans, one client reduced there heating costs by 30%.
Aerospace and Automotive Applications
Aerospace and automotive sectors widely use thermography. It’s applied in quality control and performance testing.
In car manufacturing, it checks weld quality and finds defects in body panels. This method surpasses traditional approaches in speed and reliability.
Aerospace takes it further. Thermal imaging assesses composite material health, tests de-icing systems, and evaluates engine performance. It’s crucial for safety and efficiency.
Thermal Imaging: Limitations and Challenges
Thermography isn’t perfect. It has quirks and constraints. Factors like ambient temperature, humidity, and wind can affect readings. Reflective surfaces can be hard to interpret accurately.
Proper training is vital. I’ve witnessed engineers misinterpret thermal images, leading to expensive mistakes. Understanding what you see matters as much as operating the camera.
Some situations limit thermal imaging’s effectiveness. It can’t penetrate walls or detect deep structural issues. While powerful, it shouldn’t be the only tool in use.
Future Trends in Thermography
Thermography’s future looks promising. We’re seeing higher resolution and more sensitive cameras. AI-assisted analysis speeds up interpretation and improves accuracy.
One trend I’m following is the integration of thermography with other diagnostic tools. Combining thermal data with vibration analysis or ultrasound provides a more comprehensive view of system health.
Implementing Thermography Effectively
Using thermography well involves more than buying a camera. Here are key practices I’ve developed:
- Prioritize training. Proper certification ensures accurate image interpretation.
- Select appropriate equipment. Match the tool to your specific needs.
- Create baseline readings. You should know what “normal” looks like to identify abnormalities.
- Use multiple diagnostic methods. Thermography works best alongside other tools.
- Create clear reporting systems. Consistent documentation tracks changes over time.
- Maintain and calibrate equipment regularly. Accuracy depends on well-kept tools.
- Factor in environmental conditions. You should always consider ambient factors when interpreting results.
- Use suitable analysis software. Creating a report and analysing images can be quite time consuming. Using the right analysis software can save significant time.
Thermography’s Role in Modern Engineering
Thermal imaging has reshaped our approach to engineering challenges. It’s enhanced safety, efficiency, and reliability. From predicting failures to improving energy use, its impact is significant.
As an engineer and consultant, I’ve witnessed how this technology drives improvements across industries. It offers new perspectives on our systems and structures.
Engineering’s future will likely feature technologies like thermography prominently. As we tackle energy efficiency, safety, and sustainability challenges, tools providing deeper system insights will prove invaluable.
Thermography reveals more than heat patterns. It uncovers opportunities for improvement. It helps prevent problems, optimize system performance, and expand engineering possibilities.
I’m eager to see how this technology evolves and what new applications emerge. Undoubtedly, thermography will remain a crucial engineering tool for years to come.