Quick changeover is one of the most powerful efficiency improvements in manufacturing. I’ve watched it completely reinvent production lines by minimizing downtime and increasing output. By using SMED principles, you can often cut setup times from hours to mere minutes. That’s more products shipped and less time wasted. Sound interesting? Then let’s discuss quick changeover and how you can apply it to your facility.
Understanding Quick Changeover and SMED
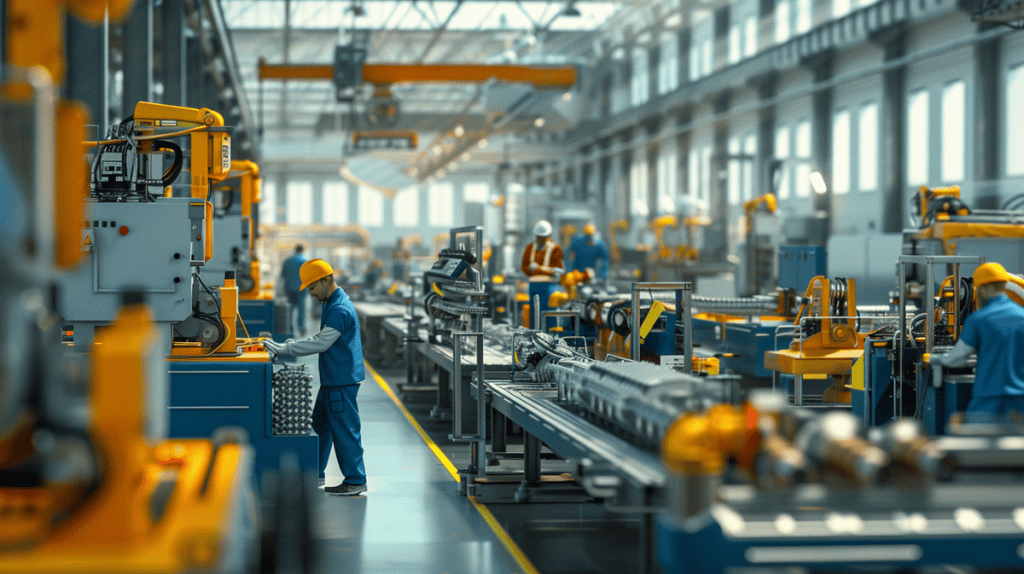
Quick changeover is another key manufacturing concept. It specifically refers to reducing the time it takes to switch from producing one product to another. I’ve witnessed how quick changeover can transform manufacturing lines.
The methodology behind quick changeover is SMED (Single-Minute Exchange of Die), which Shigeo Shingo developed in Japan during the 1960s and 1970s. The objective of SMED is to reduce the time it takes to change production line setups to less than 10 minutes.
The main advantages of employing quick changeover methodologies are:
- Greater manufacturing line flexibility
- Lower inventory levels
- Higher product quality
- Reduced manufacturing costs
- Better ability to serve customers
Quick changeover is particularly important in industries such as automotive, electronics, and food processing. It’s also particularly relevant if you have high product variety and demand variability.
For example, I once worked with a company that manufactured cars. They were struggling with long setup times when transitioning from producing one model to another. We applied SMED principles, and we were able to reduce the setup times by 70%. The impact on their business was massive.
The Cost Impact of Changeover Time
Let’s do the math. Production downtime is costly. I’ve seen companies lose tens of thousands of dollars per hour when machines sit idle.
Here’s a specific example I came across:
A factory produces a $0.50 component. They have 4 changeovers daily, and each takes 30 minutes. Here’s the math on annual costs:
- 4 changeovers * 30 minutes = 2 hours downtime per day
- 2 hours * 250 working days = 500 hours annual downtime
- Factory billing rate: $100 per hour
- Annual cost: 500 hours * $100 = $50,000
That’s $50,000 lost annually over a $0.50 part! This doesn’t include the hidden costs of:
- Excess inventory
- Lower ability to flex
- Longer lead times
- Quality issues due to rushed setups
Quick changeover is nothing more than lean manufacturing. It eliminates waste, improves flow, and makes the entire operation more efficient.
Implementing Quick Changeover: Step-by-Step Approach
Implementing quick changeover isn’t a one-day task. For me, a typical workshop is 2-3 days. Here’s the step-by-step process I follow:
- Analyze the way they currently do changeovers.
- Figure out what setup steps can be external and what steps have to be internal.
- Change internal steps to external steps.
- Combine internal steps as much as possible.
- Standardize and document everything.
Internal steps are anything that has to happen when the machine is stopped. External steps are anything the operator can do while the machine is running. The overarching goal is to make everything possible an external step.
One company that stands out was a printing company. We turned ink mixing from an internal step to an external step, and that one change reduced their changeover time by 25%.
Standardization is the big challenge. Standardization is why a lot of continuous improvement efforts fail, so I’m pretty strict here. We make sure that the changes are documented and are visual changes (not just telling the operator how to do something a different way).
Tools and Techniques for Reducing Changeover Time
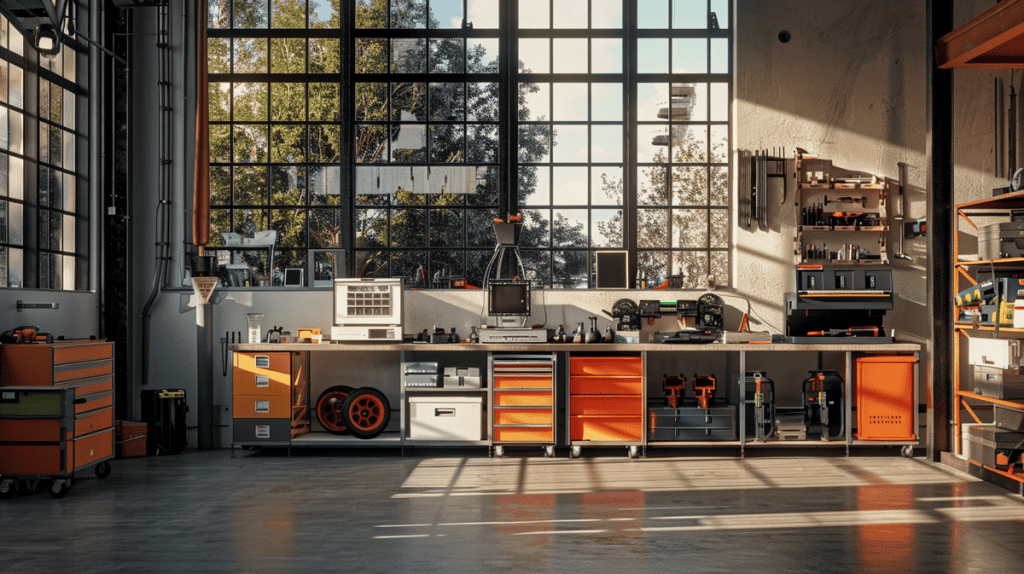
Here are some of the tools I’ve experimented with over the years to reduce changeover times:
Quick release mechanisms: Convert bolts to clamps or magnets
Color coding: Match colors from a part to a position
Pre-set controls: Set the controls before downtime
Modular equipment: Build a different part that can be swapped out on the equipment
Parallel processing: Have multiple people working at once
Checklists: Write a checklist so the changeover is done the same way every single time
Technology also helps. I use software to track changeover times and find bottlenecks. Some companies use augmented reality to help operators set up complex parts.
The key takeaway is to make the changeover foolproof. This eliminates mistakes and variability.
Quick Changeover Success Stories Across Industries
Quick changeover isn’t just for manufacturing. I’ve used these same principles in the following industries:
Automotive:
- Reduced stamping press changeover from 2 hours to 15 minutes
- How: Standardized die heights, quick release clamps, pre-heating of dies
Banking:
- Reduced teller station changeover from 30 minutes to 5 minutes
- How: Organized cash in drawers, standardized paperwork, and automated log in procedures
Healthcare:
- Reduced operating room changeover from 25 minutes to 10 minutes
- How: Pre-prepared kits trays, parallel cleaning steps, standardized room layouts
Education:
- Reduced classroom changeover from 10 minutes to 3 minutes
- How: Mobile equipment stations, color-coded subject materials, student transition ownership
The common thread here is standardization, preparation, and involvement from staff. These principles apply to any industry.
Quick changeover and SMED are excellent strategies to improve efficiency and reduce costs. I’ve personally witnessed these methods revolutionize operations in various industries.
Whether it’s an automotive factory or a hospital, the same basic changeover principles apply. By analyzing the processes, changing internal setup to external, and optimizing the rest of the steps, you can make a significant impact in time. The trick is standardizing, documenting, and continuously improving. With the right attitude and game plan, you too can optimize changeovers and save a lot of time.