Process optimization can transform your business operations. I’ve helped businesses double their productivity and reduce costs by 30% with process optimization. So, you might be wondering if it can do the same for you. Here’s how optimizing your processes can increase efficiency, eliminate waste, and help your business grow.
Understanding Process Optimization
Process optimization is the process of refining business operations to make them more efficient, productive, and profitable. It’s a critical strategy for businesses that want to remain competitive in today’s market – a market that continues to move faster and faster.
The core objectives of process optimization are to reduce waste, improve quality, and increase customer satisfaction.
I’ve personally seen process optimization work in virtually every industry. Manufacturers experience significant speed and quality improvements in their production facilities. Service businesses are able to significantly reduce customer wait times and increase satisfaction.
Even healthcare organizations use these same principles to make patient care more efficient and safe.
And it’s not just for massive companies, either. Small businesses also benefit from process optimization. For example, one local bakery I worked with was able to double its output without hiring a single new employee by optimizing its production process.
The secret is to take a systematic approach to analyze and improve. This isn’t just making changes for the sake of it. It’s carefully evaluating each process step to identify how to make it better.
Common Process Optimization Methodologies
Process optimization isn’t a single, standardized strategy. There are several different methodologies designed to meet various business needs:
Six Sigma, which operates under the DMAIC framework: Define the problem, Measure, Analyze, Improve, Control.
Lean management, which focuses on eliminating waste and maximizing value. It’s highly effective in manufacturing but can also be applied to other industries.
Total Quality Management (TQM), which focuses on continuous improvement and customer satisfaction. This is an all-employee philosophy from top management to the front-line worker.
Business Process Reengineering (BPR), which requires scrapping and rebuilding core processes within a business. This methodology is often used when you’ve already optimized processes and there’s no more room for incremental improvement.
Other methodologies, including theory of constraints, Kaizen, Agile, value stream mapping, 5S, PDCA, process mining, and others.
Each methodology has its own strengths. The best methodology for you depends on your unique business needs and problems.
Steps to Identify and Analyze Processes
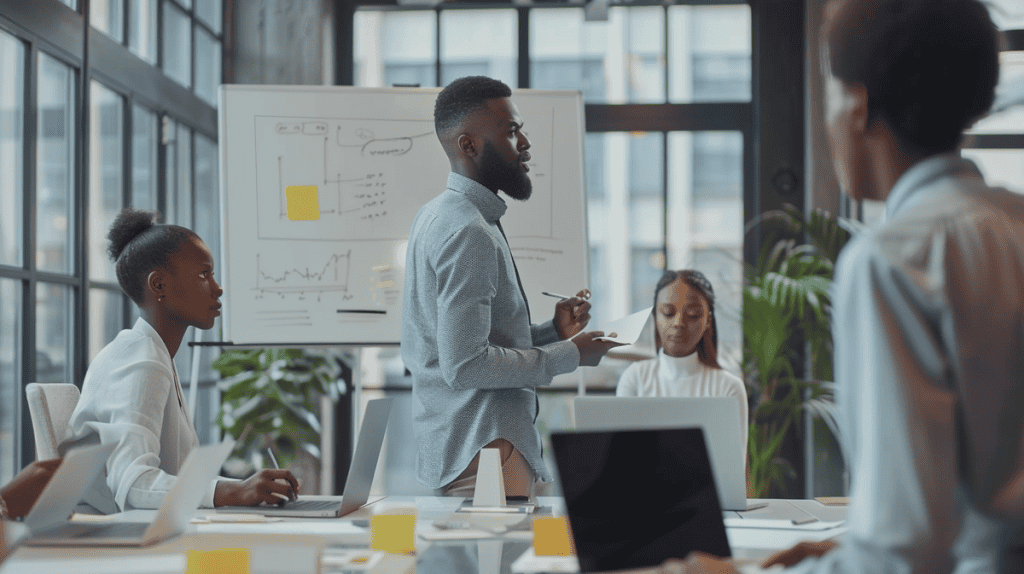
Understanding your current operations is the first step to effective process optimization. Here’s how to get started:
Map your current processes: Mapping out your processes visually helps you identify inefficiencies and bottlenecks. I personally like to use flowcharts or swimlane diagrams to map processes.
Gather and analyze data on your processes: This might involve time studies, quality data, or customer feedback. Data is objective and will tell you exactly where you can improve your processes.
Prioritize the processes you want to optimize: You can’t optimize every process all at once. Select the highest-impact processes that need to be optimized to improve your bottom line and customer satisfaction.
Include your team in the analysis: Frontline employees likely have useful insights into process inefficiencies. Their buy-in is also critical to successful process optimization.
Keep in mind that this is an iterative process. You will need to continually revisit and refine your strategy as your business changes.
Techniques for Improving Efficiency
If you discover areas where processes aren’t as efficient as they could be, there are several techniques you can use to make them more efficient.
Value stream mapping is a process visualization technique that shows the flow of materials and information as they transform into a product or service for a customer. This is an excellent way to identify non-value-added steps in a process.
Root Cause Analysis is a technique to identify the deep, underlying problems causing frequent inefficiencies. One of the simplest and most effective root cause analysis techniques is the “5 whys.”
Waste elimination is a core concept of lean management. It involves identifying and eliminating any step in a process that doesn’t add value to the customer.
Standardization ensures that a process is conducted the same way each time. This reduces errors and makes it easier to train employees. I’ve seen standardization cut training time in half for some of our clients.
Automation is a great way to improve efficiency for any repetitive task. However, be sure to optimize the process before automating. If you don’t, you’ll end up with a more efficient version of an already inefficient process.
Process Optimization in Manufacturing
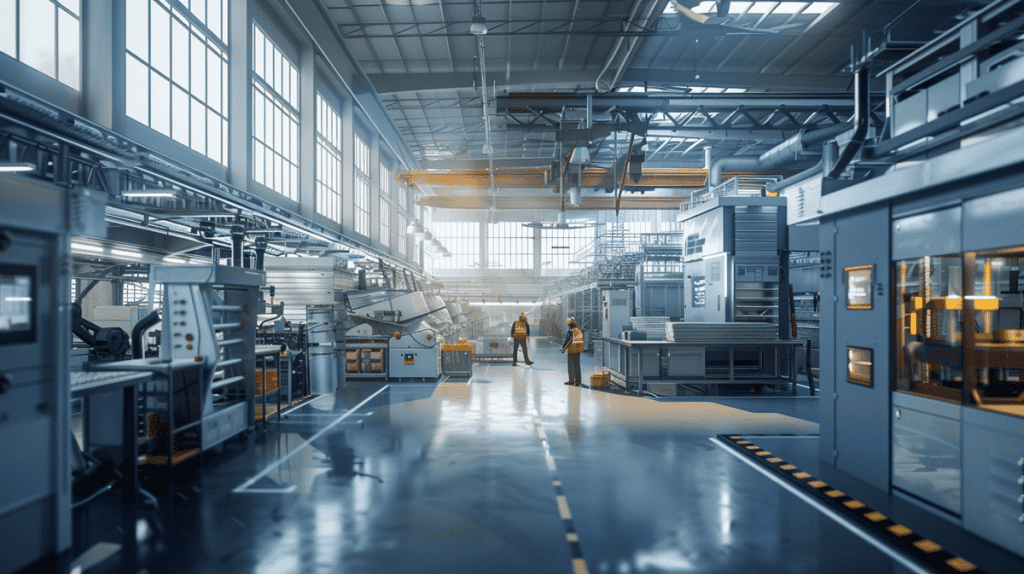
Manufacturing settings have some unique process optimization opportunities and challenges.
In processing facilities (e.g., chemical plants, oil refineries), over 35% of the control loops have issues. A single facility might have hundreds or even thousands of controls loops. Optimizing each of these loops can create a step change improvement in facility efficiency and product quality.
Optimizing the loops in a processing plant can increase efficiency and product quality.
On a production line, optimizing the balance between workstations can eliminate bottlenecks. For example, I once worked with a car manufacturer that increased production by 20% with a simple improvement to how the assembly line was balanced.
Improving quality control can also have a big impact on reducing defects and rework. Statistical process control is a key tool here, which helps you catch and eliminate problems before they lead to defective products.
Optimizing inventory management can significantly reduce the working capital investment tied up in stored inventory.
Improving equipment efficiency often means setting up a basic preventive maintenance program, which eliminates any unexpected downtime from the equipment and extends its useful life.
Tools and Software for Process Optimization
Mostly, process optimization today involves using various tools and software.
Process mapping software, such as Lucidchart or Microsoft Visio, is useful for creating visual representations of your processes. These visuals are critical for identifying ways to optimize the processes.
Data analysis tools, like Minitab or SAS, are helpful when working on a Six Sigma project. You can use these tools to parse through large data sets and find statistically significant trends.
Simulation and modeling software allows you to virtually test changes to a process before rolling those changes out in the real world. This saves time and resources.
Project management software, like Trello or Asana, ensures everyone knows what they need to get done and by when. It also keeps your optimization project on track.
Automation tools can also be a big part of optimizing a process, including:
- RPA (Robotic Process Automation) software
- Workflow automation solutions
- AI that makes decisions based on data
- IoT devices to collect real-time data. Selecting the right tool for each task will save time when optimizing a process.
Key Performance Indicators (KPIs) for Process Optimization
Measuring how effectively you’ve optimized a process requires selecting the right KPIs.
KPI | Description |
---|---|
Cycle Time | Time it takes to complete one unit of production or service |
First Pass Yield | Percentage of products produced correctly the first time |
Overall Equipment Effectiveness (OEE) | A measure of how productive manufacturing equipment is |
Customer Satisfaction Score (CSAT) | A measure of customer satisfaction with a product or service |
Cost per Unit | Total cost of making the products divided by the number of products |
Employee Productivity | How much a single employee or labor hour can output |
Inventory Turnover | How quickly you sell and restock products |
These KPIs will give you a well-rounded view of your process’s performance. They also allow you to track your improvements and see where the process still needs further optimization.
The benefits of process optimization
Process optimization can completely revolutionize your business operations. Here are the main benefits:
- Increased operational efficiency: Optimizing processes reduces waste and increases output.
- Cost savings: Identifying and eliminating inefficiencies often saves a significant amount of money.
- Improved product/service quality: When you optimize processes, you produce fewer defects and errors.
- Increased customer satisfaction: Receiving products/services faster and with higher quality makes customers happier.
- Competitive advantage: If you can operate more efficiently, you can generally afford to charge lower prices.
- Employee satisfaction: Optimized processes often make employees’ jobs easier and more enjoyable.
I’ve personally witnessed companies achieve incredible results through process optimization. One manufacturer reduced their production costs by 30% and simultaneously produced a higher quality product.
Another service business decreased customer wait times by 50% and consequently received an increase in customer satisfaction scores by 20%.
Challenges of Implementing Process Optimization
Although the benefits are great, process optimization has its challenges:
- Change resistance: Employees may be resistant to changing the way they’ve always done things.
- Resource limitations: Optimization often requires resources, such as time and money.
- Lack of expertise: Successful optimization requires specific expertise and skills.
- Sustaining change momentum: People might feel less excited if the work is no longer easy.
- Balancing short-term pain with long-term gain: Changes will likely lower productivity in the short term.
To address these challenges, you’ll need to plan carefully, communicate effectively, and ensure you have strong leadership buy-in.
Best Practices and Tips for Successful Process Optimization
Here are the best practices I recommend based on my experience optimizing processes:
Get leadership buy-in. If senior leadership doesn’t support your initiative, your process optimization efforts will likely fail.
Ensure effective communication. You need to ensure that employees understand why processes are changing and how they will benefit.
Provide proper training for your employees. They need the skills to execute and maintain the new processes.
Create a culture of continuous improvement. Encourage employees to always look for ways to improve the process.
Use data to make decisions. Don’t rely on gut feelings or opinions to optimize processes.
Regularly audit optimized processes. Just because a process is optimized today doesn’t mean it will be next month. You need to be diligent and willing to optimize things even further.
Finally, remember that process optimization is a journey, not a destination. It’s an ongoing task, and a challenging one at that. However, it can deliver significant returns.
Lean startup principles can also help you optimize processes to accomplish more with less.)
Closing out
Process optimization is one of the most effective strategies businesses can use to make their operations more efficient, lower costs, and increase quality. I’ve witnessed the results of these methodologies in any industry you can think of.
Identifying bottlenecks, simplifying processes, and making decisions based on data, you can make massive strides. The key takeaway is that optimization is a never-ending process.
If you dedicate yourself to continuous improvement, you’ll enjoy the long-term rewards in the form of increased productivity, customer satisfaction, and competitive edge.