As an engineer with over two decades of experience in condition monitoring, I’ve witnessed the effect maintenance strategies have on industrial operations. Predictive maintenance and preventive maintenance are both excellent options to minimize downtime and prolong the life of your equipment. I often get asked the question Predictive vs preventive maintenance.
So how do you know which one is best? It’s not always a clear-cut answer. So let’s discuss the main differences in this post and help you determine how you should approach maintenance.
Understanding Predictive and Preventive Maintenance
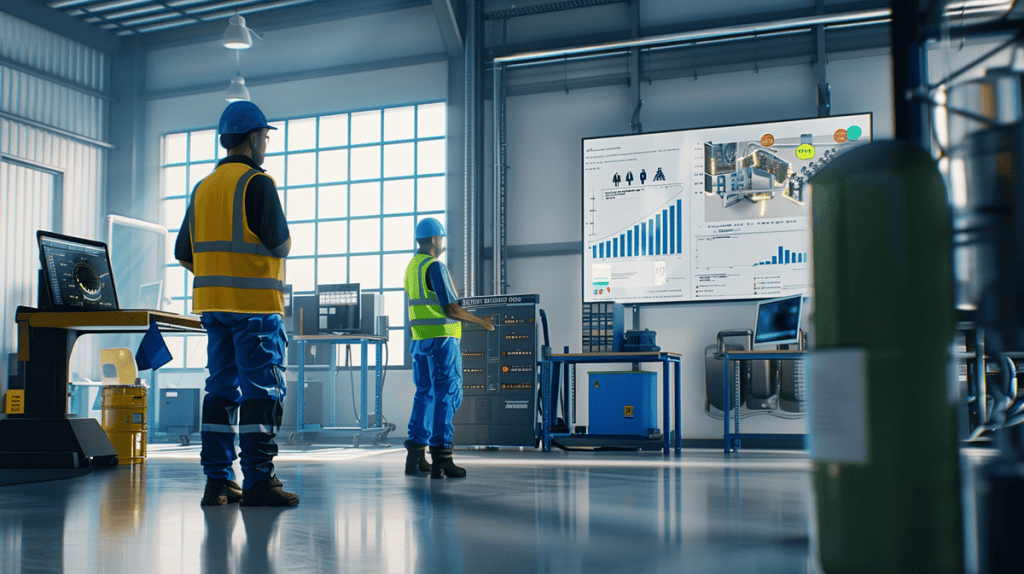
Predictive maintenance and preventive maintenance are two different ways to maintain equipment. Predictive maintenance relies on data and analytics to predict when equipment will fail. Preventive maintenance is general maintenance performed at regular intervals to prevent equipment from failing. These maintenance strategies differ in when and how you take care of equipment.
Maintenance strategies in industrial settings have evolved over time. Traditional reactive maintenance evolved into preventive maintenance, and now predictive maintenance is becoming more common. This evolution is designed to reduce downtime and maximize resources.
I’ve seen the impact of downtime in manufacturing plants firsthand, and it’s massive. The average manufacturer experiences about 800 hours of downtime per year. That’s more than a month of lost productivity! This is a huge reason why choosing the right maintenance strategy is critical.
Both of these maintenance strategies have their place in modern maintenance programs. The strategy you choose depends on various factors, including the type of equipment, how much it costs, and how critical it is to your operation. By understanding these maintenance strategies, you can make an informed decision about your maintenance strategy.
Predictive Maintenance: A Deep Dive
Predictive maintenance uses real-time data to predict when equipment will fail. It leverages advanced technology to monitor machine health and performance. The objective is to only perform maintenance when it’s needed.
The primary technologies used in predictive maintenance are:
- Sensors and IoT devices
- Data analytics and machine learning
- Condition monitoring systems
- Vibration analysis tools
Each of these technologies captures and analyzes data in real time. They then look for patterns that suggest a machine is on the cusp of failing. If so, you can proactively schedule maintenance to ensure the machine doesn’t fail.
The most common predictive maintenance KPIs are equipment uptime, mean time between failures, and maintenance expenses. These three KPIs help you determine if the predictive maintenance strategy is effective.
In my consulting work, I’ve encountered predictive maintenance success stories. Standard results from predictive maintenance are a 35-50% reduction in equipment downtime. This is a massive win for the organization’s profitability.
Preventive Maintenance: A Comprehensive Look
Preventive maintenance is the practice of performing regular scheduled maintenance tasks to avoid equipment failures. The idea with this approach is that maintenance can prevent equipment failures from happening. There are a few different types of preventive maintenance:
- Time-Based Maintenance
- Usage-Based Maintenance
- Failure Finding Maintenance
Time-based maintenance involves tasks completed at specific intervals. Usage-based maintenance involves maintenance triggered by equipment runtime or cycle count. Failure finding maintenance involves inspecting standby equipment for hidden failures.
The key to preventive maintenance is scheduling and planning. You must plan maintenance tasks at scheduled times to minimize any disruption to operations. Most companies use preventative maintenance software to manage all of this.
I’ve observed that the benefits of preventative maintenance can be significant. You may see a 20-40% increase in asset life span. Extending the life of an asset by even just a few years can result in tens of thousands of dollars in savings.
Cost Implications of Predictive vs Preventive Maintenance
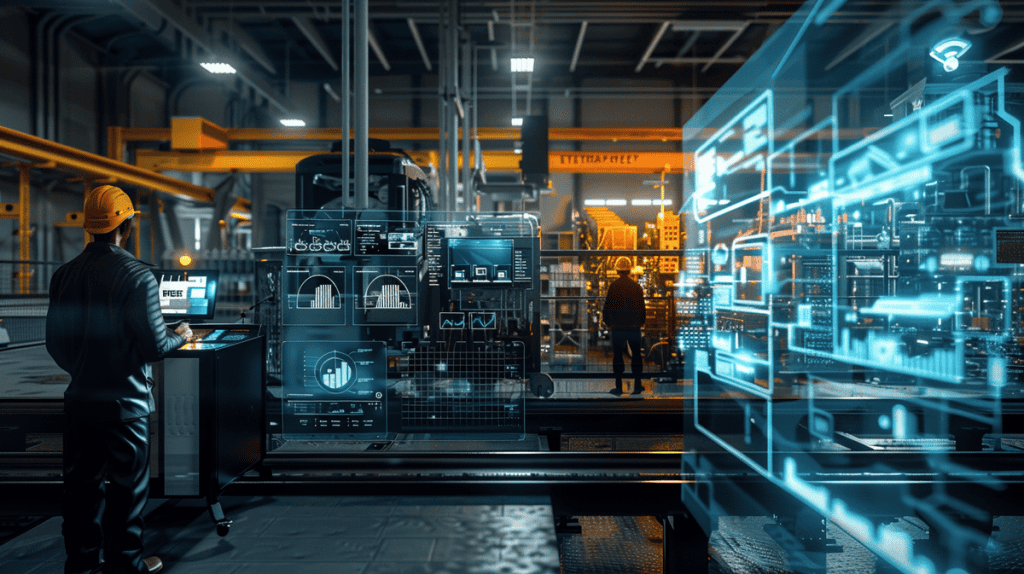
The cost considerations of predictive maintenance and preventive maintenance are quite different. Predictive maintenance often has a higher initial investment. You need specialized sensors, data analysis software, and skilled labor. Preventive maintenance generally has lower upfront costs, although this strategy could incur more significant long-term expenses.
Cost Consideration | Predictive Maintenance | Preventive Maintenance |
---|---|---|
Initial investment | High | Low to medium |
Ongoing costs | Medium | High |
Downtime costs | Low | Medium |
Parts replacement | As needed | On a schedule |
The ROI of predictive maintenance can be incredibly high. In fact, I’ve heard of situations where it produced 10 times the ROI as traditional methods. The reason it’s so profitable is because of less downtime and more efficient resource allocation.
However, the potential cost savings of predictive maintenance may vary by industry. Predictive maintenance is most valuable to companies in the manufacturing and energy sectors. Other service industries may find preventive maintenance is the better choice.
Implementation Challenges and Solutions
Predictive maintenance is difficult to execute. It requires significant process and culture change. Data quality and integration are the most common challenges. Many companies find predictive maintenance too technically complex.
Preventative maintenance also has its own challenges. Aligning maintenance schedules and allocating resources can be a major challenge. There’s also a risk of doing too much preventative maintenance and generating unnecessary costs.
The most common strategies to address these challenges are:
- Piloting the program, starting with critical equipment
- Creating comprehensive training plans for the maintenance team
- Integrating the system with the rest of the IT infrastructure
- Regularly reviewing and adjusting the maintenance strategy
I’ve seen companies use these strategies to make preventative maintenance work. For example, one manufacturer reduced overall maintenance costs by close to 30% by doing just that.
Predictive Vs Preventive Maintenance Choosing The Right One
The maintenance strategy you choose will depend on various factors, including your industry, types of equipment, and business objectives. The criticality of each asset is another key factor to consider.
You can use a decision-making framework like:
- Asset criticality assessment
- Cost-benefit analysis of each strategy
- Evaluation of your existing maintenance capabilities
- Data quality and availability assessment
Keep in mind there isn’t a one-size-fits-all solution as you may use a mix of predictive and preventive maintenance on different types of equipment.
For a more in-depth breakdown of how to select a maintenance strategy, you can find a link to a comprehensive maintenance strategy selection guide here. [link to the maintenance strategy selection guide].
Emerging Trends in Maintenance Strategies
The future of maintenance is very promising. We’re seeing more IoT and AI integration in maintenance operations. These technologies are making predictive maintenance more effective and more accessible.
Condition monitoring is also improving. New sensors can identify a wider variety of potential issues, which makes maintenance predictions more accurate.
We’re also seeing a lot of innovation in predictive maintenance thanks to Industry 4.0. In smart factories, interconnected systems are optimizing maintenance tasks. This level of integration is making maintenance more efficient than ever before.
The potential value of these advancements is huge. The McKinsey Global Institute estimates that if predictive maintenance is implemented on a broad scale in manufacturing, the industry could save $240-$627 billion. That’s a staggering figure and a great example of why it’s so important to keep up with the latest maintenance strategies.
wrapping it up
Predictive and preventive maintenance techniques are essential for today’s industrial businesses. I’ve experienced the power of these strategies to reduce downtime and extend the life of equipment. Predictive vs preventive maintenance comes down to your particular requirements and resources. As technology continues to evolve, maintenance will become even more data driven and effective.
Keep in mind that the right strategy can save you a lot of money and make your operation more productive. Assess your current maintenance strategy and think about making an upgrade to remain competitive.