Errors. They’re the bane of every industry because from assembly lines to operating rooms, mistakes cost money, time, and sometimes lives. But what if we could stop errors before they happen? That’s the promise of poka yoke. In this article, we’ll explore poka-yoke examples across industries.
We’ll dive into real-world examples. We’ll unpack design principles and look at cutting-edge digital solutions. I’m hoping by the end, you’ll see why I’m so passionate about this approach.
I’ve spent decades in lean management. I started on the factory floor and worked my way up. Presently I help businesses across sectors implement lean practices. One key CI tool I always use is poka-yoke it can have significant impact when done correctly.
Poka-yoke is a Japanese term for “mistake-proofing.” A Simple concept with powerful results. It’s about designing processes that make errors nearly impossible. It’s a proactive and not reactive approach that works.
We’re about to jump into a world of error-proofing. It’s not just about preventing mistakes the core principle is about creating robust, efficient systems. It’s also about empowering workers and driving continuous improvement.
That said let’s get started.
Manufacturing Poka-Yoke Examples
Let’s kick things off with manufacturing Poka-Yoke Examples to begin with. As I mentioned It’s where I cut my teeth. Assembly lines are ripe for errors. But they’re also fertile ground for poka-yoke solutions. Here’s some examples:
- Color-coded connectors: Different colored plugs and sockets to prevent incorrect connections
- Asymmetrical parts: Components designed to fit together only in the correct orientation
- Jigs and fixtures: Custom-made tools that hold parts in the correct position during assembly
- Barcode scanning: Verifying correct parts and materials before assembly begins
- Count sensors: Ensuring the right number of components are present before proceeding
- Shape-coded containers: Bins and trays shaped to match specific parts, preventing mix-ups
- Sequential operation systems: Machines that only allow steps to be performed in the correct order
- Error-proofing software: Programs that flag potential mistakes or inconsistencies in data entry
- Go/no-go gauges: Simple tools used to quickly check if a part meets specified dimensions
lets take a closer look at a couple from above.
During parts installation I’m sure we’ve all seen misaligned components. It can be a costly mistake. However smart design can prevents this. Asymmetrical shapes ensure correct orientation and connectors with unique shapes prevent mismatches. These are simple, but effective things that can be implemented.
One simple tool that can be used is color coding. It’s visual and intuitive enabling workers to quickly identify correct parts thus It reducing cognitive load. This intern reduces Mistakes as a result.
Warehouse Poka-Yoke Examples
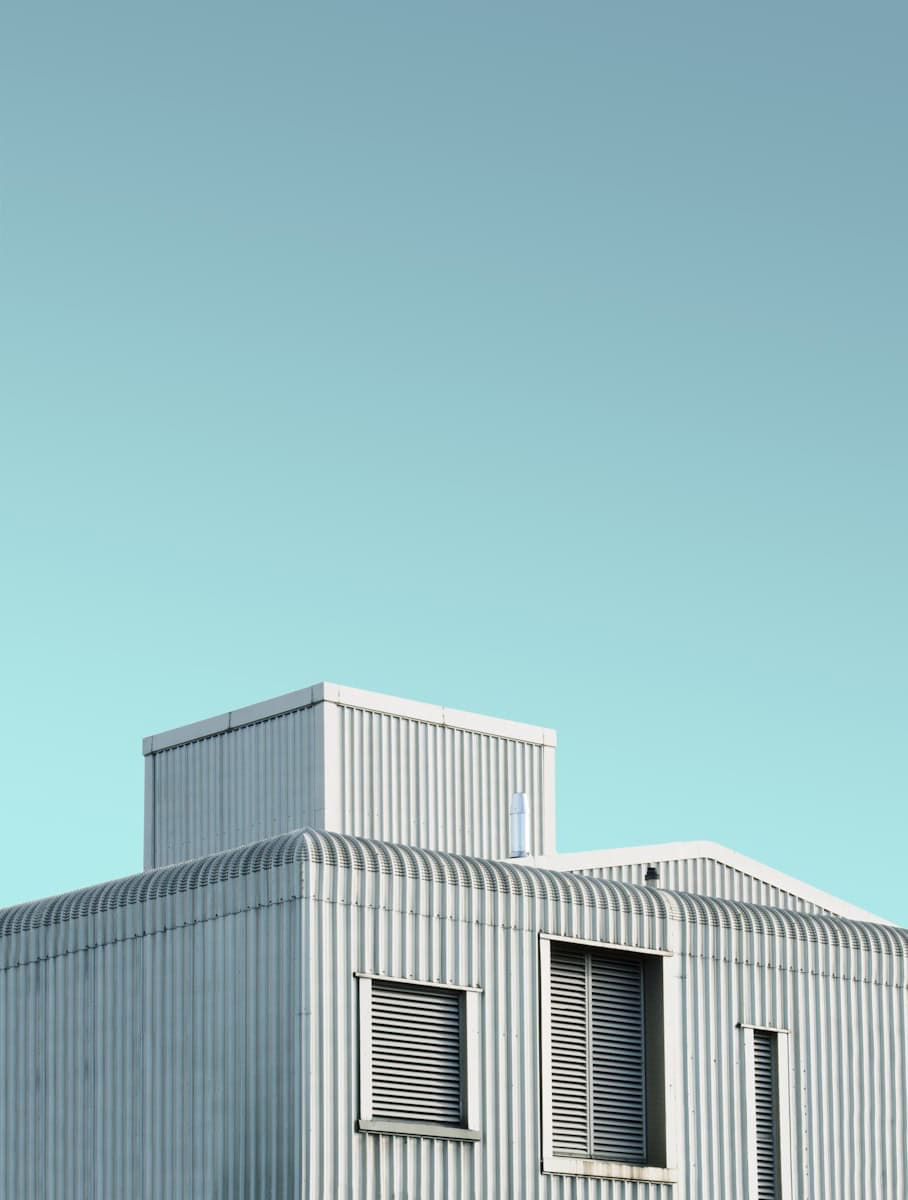
Warehouses for anyone who hasn’t worked in one may seem simple but as most know in the industry there complex beasts. They have the potential to be ripe with errors. This makes them prime candidates for poka-yoke.
- Pick-to-light systems: LED lights indicate correct bin locations for order picking
- Barcode scanning: Verifying correct items and quantities during picking and packing
- Voice-directed picking: Audio instructions guide workers to correct locations and quantities
- Color-coded zones: Different colored floor markings or shelving for easy identification of areas
- RFID tagging: Automatic tracking of inventory movement and location verification
- Weight-based counting systems: Scales that verify correct quantities based on item weight
- Dimensioning systems: Automated measurement of package dimensions to ensure correct sizing
- Put-to-light systems: LED-guided placement of items in the correct locations for sorting or packing
- Automated sorting systems: Conveyors and scanners that route items to the correct destinations
- Visual management boards: Clear, visual displays of inventory levels, order status, and workflow
Lets take a deeper look at a couple of above.
Barcode scanning is common place now and for good reason because It slashes picking errors. Workers will generally scan items and locations giving them clear acknowledgement its the correct location. It’s a simple yet powerful safeguard.
Color-coded storage areas take this further. it provide visual cues and help can workers quickly identify zones. This in turn reduces confusion and speeds up processes. As a affect Efficiency and accuracy both improve.
Office Environment Examples
Offices aren’t immune to errors. They just look different to a warehouse or manufacturing plant with regards to poka-yoke. That said the same principles still apply.
- Document version control: Software that automatically tracks and manages document revisions
- Email confirmation prompts: Pop-up alerts asking to confirm before sending emails with attachments
- Automated data backup: Systems that regularly and automatically save work to prevent data loss
- Calendar scheduling assistants: Software that checks for conflicts before booking meetings
- Form field validation: Automatic checks for correct data format in online forms (e.g., email addresses)
- Color-coded filing systems: Different colored folders or labels for easy identification of document types
- Standardized document templates: Pre-formatted files to ensure consistent layout and information
Let look at a couple of examples from above,
Form field validation is crucial. for user input is a tried and tested process. It catches data entry errors and also prevents incomplete submissions. . It’s a digital safety net on data entry.
Standardized document templates are underrated. They ensure consistency and guide users through processes. They reduce errors and cognitive load. It’s poka-yoke in document form.
Healthcare Strategies
Healthcare errors can be catastrophic this poka yoke here is literally life saving.
- Barcode medication administration: Scanning patient wristbands and medication to ensure correct drug and dosage
- Surgical timeout procedures: Mandatory pre-surgery checklists to verify patient, procedure, and site
- Electronic health records (EHR) with built-in alerts: Systems that flag potential drug interactions or allergies
- Automated dispensing cabinets: Secure medication storage that tracks inventory and access
- Patient identification wristbands: Multiple identifiers (name, DOB, ID number) to prevent misidentification
- Standardized order sets: Pre-defined medication orders to reduce prescribing errors
- Fall prevention alarms: Bed or chair sensors that alert staff when at-risk patients attempt to stand
- Single-use devices: Disposable medical instruments to prevent cross-contamination
- Computerized physician order entry (CPOE): Digital prescription systems to eliminate handwriting errors
Medication dispensing systems are critical. They prevent dosage errors. They ensure right patient, right drug. Barcode scanning adds another layer of safety. It’s a multi-stage approach.
Patient identification protocols are non-negotiable. Wristbands with barcodes are standard now. They’re scanned before procedures. It prevents mix-ups. It’s a simple yet crucial safeguard.
Examples In The Service Industries
Service industries aren’t immune to errors. They just manifest differently. But poka-yoke still applies. some Poka-Yoke Examples are,
In hospitality, checklists reign supreme. Room cleaning protocols ensure consistency. They prevent oversights. It’s simple yet effective poka-yoke.
Retail benefits from point-of-sale systems. They prevent pricing errors. They ensure accurate inventory tracking. It’s technology-enabled poka-yoke.
Customer support uses scripted responses. They ensure accuracy and completeness. They prevent misinformation. It’s poka-yoke for communication.
But here’s the rub: service is inherently human. Poka-yoke shouldn’t replace empathy. It should enhance it. Design solutions that support, not constrain, human interaction.
Design Principles of Effective Poka-Yoke
Effective poka-yoke isn’t rocket science. But it does require thoughtful design.
Simplicity is key. Complex solutions create new problems. They confuse users. Keep it straightforward. Make it intuitive.
Immediate feedback is crucial. Users need to know instantly if there’s an error. Delayed feedback allows mistakes to compound.
Low implementation cost is important. Expensive solutions face resistance. They’re hard to justify. Aim for high impact, low cost. It’s the sweet spot for poka-yoke.
But here’s a trap to avoid: don’t design in isolation. Engage users throughout the process. Their insights are invaluable and they’ll spot potential issues you might miss.
Digital Poka-Yoke Solutions
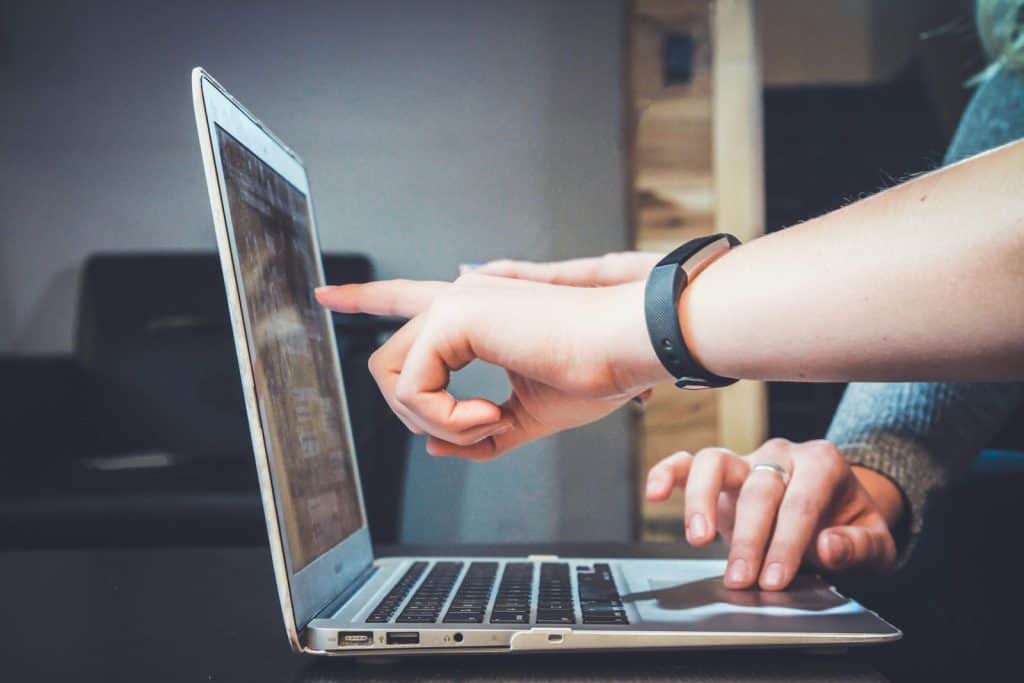
Digital solutions are revolutionizing poka-yoke. They’re powerful and versatile.
AI-driven quality control is a rapidly being utilised in all industries. It can spot patterns humans miss and has the ability to predict potential errors. It’s proactive poka-yoke.
Smart device integrations prevent errors in real-time. Stuff like IoT sensors flag issues instantly. They prevent small problems from becoming big ones. It’s poka-yoke at the edge.
Augmented reality guides workers through complex tasks. It overlays instructions in real-time. It prevents errors in assembly and maintenance. It’s next-gen poka-yoke.
But here’s a word of caution: technology isn’t a magic wand It’s a tool. Effective implementation requires careful planning. It needs user training and support. Don’t underestimate the human factor.
Measuring Poka-Yoke Effectiveness
Measuring poka-yoke impact is crucial. It justifies investment. It guides improvement.
Error rates are an obvious metric. Track them before and after implementation. The difference is your impact, and is a clear quantifiable measure.
Cost savings are always powerful. Calculate the financial impact of prevented errors. It’s a language management understands and helps justify further investment.
Employee satisfaction is often overlooked but it reduces stress and boosts confidence. Happy workers are productive workers. Don’t ignore this metric.
One key takeaway is don’t just measure, act on the data! When carrying out any Continuous improvement is key. Use metrics to refine your poka-yoke strategies. It’s an ongoing process.
In conclusion, poka-yoke isn’t just about preventing errors. It’s about creating robust, efficient systems that support workers and drive continuous improvement.
- Implement it wisely and engage your workforce.
- Keep it simple and measure your impact.
You’ll see transformative results. That’s the power of poka-yoke.