I’ve been involved in lean management for decades. I’ve witnessed a staggering amount of transformations. These have ranged from the brilliant, the disastrous and the utterly chaotic. My career in lean transformation started for me in my humble start on the production line and progressed to launching my own consulting firm.
I’ve discovered that embracing lean isn’t just about deploying tools and techniques. It’s about radically overhauling an organization’s very DNA. So, follow me as we plunge into the nitty gritty of fostering a lean culture that truly shines.
Assessing Current Organizational Culture
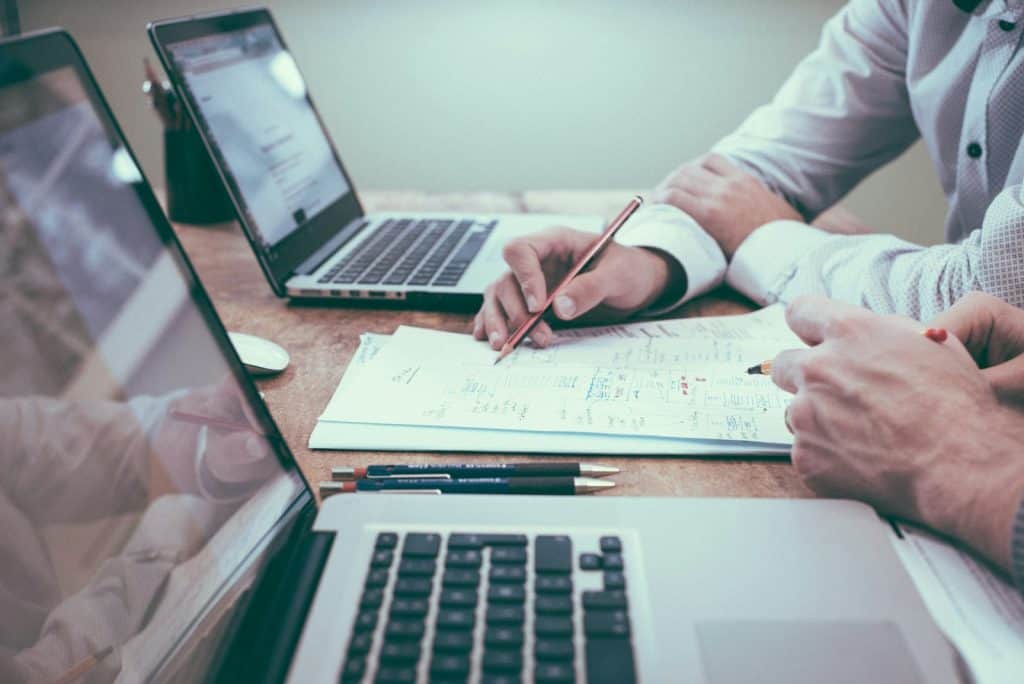
Before we look into the principles of lean management, it’s crucial to recognize the initial state. Many organizations I’ve observed present a blend of effective practices and counterproductive habits. To achieve success, you must identify the problematic areas and anticipate the obstacles that may impede your progress in the future.
A good initial step is to Begin with a site walkthrough – venture out and observe firsthand. You shouldn’t just consult with managers; engage and discuss with frontline personnel. They’ll provide insights on operational efficacy and shortcomings. Be vigilant for indications of the “that’s the way we have always done it” mentality. It’s an indicator of potential resistance to change.
pro tip: Pay close attention to frontline managers. These individuals often possess the capacity to significantly impact the success of your lean initiatives.
Leadership Buy-In and Commitment
Here’s the tough truth people often miss: if the C-suite isn’t on board, you’re dead in the water. I’ve seen countless lean efforts fizzle out because leadership treated it like a flavour-of-the-month program rather than a fundamental shift in how they do business.
To get that crucial buy in, you need to speak their language. Don’t be poetic about the philosophy of lean; show them the money. Present case studies of similar companies that have reaped the benefits of lean. Better yet, start with a pilot project that demonstrates quick wins.
Remember, leaders need to do more than just nod along in meetings. They need to walk the talk. Get them involved in kaizen events, have them participate in daily stand-ups. When employees see the boss rolling up their sleeves, it sends a powerful message.
Lean Transformation Employee Engagement and Education
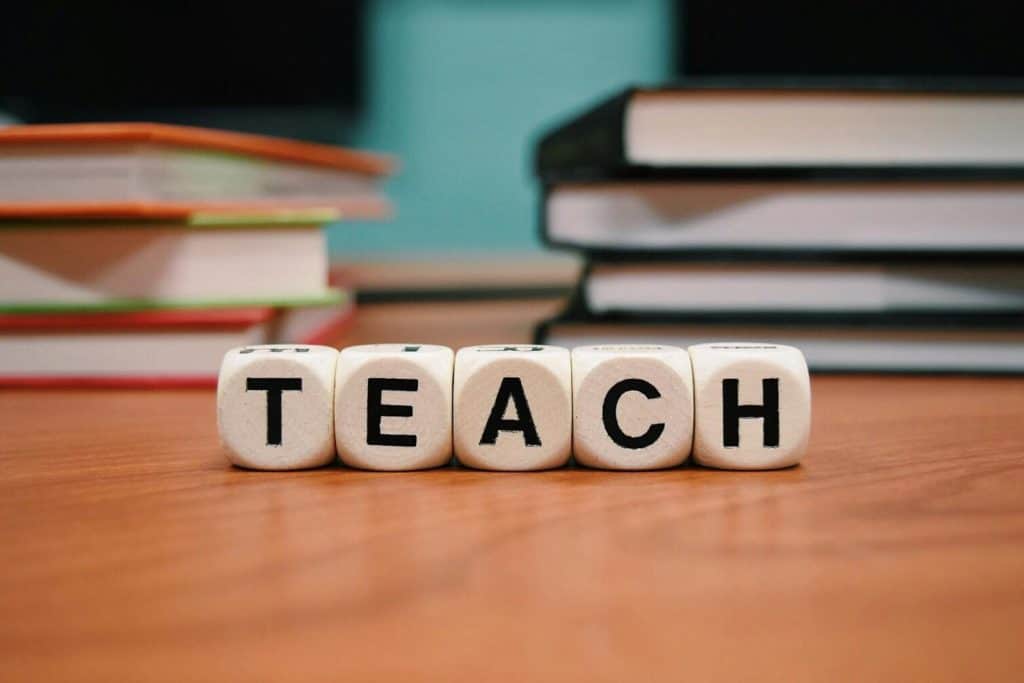
Now, one of the most important and the lifeblood of any lean transformation: your workforce. You can’t just drop a bunch of lean jargon on them and expect miracles. You need to bring them along for the ride.
Start with the basics. Explain what lean is (and isn’t) in plain language everyone can understand. Address the elephant in the room: job security. I’ve found that being upfront about how lean can make their jobs easier and more fulfilling goes a long way in alleviating fears.
One other key factor is training, but don’t just rely on classroom sessions. Get hands-on. Use simulations and real-world problem-solving exercises. Make it relevant to their daily work. And for Pete’s sake, make it engaging. Nothing kills lean enthusiasm faster than death by PowerPoint.
Implementing Lean Transformation Tools and Methodologies
Alright, time to get our hands dirty with some lean tools. But here’s a key issue don’t fall into the trap of thinking that implementing a few tools makes you lean. It doesn’t.
That said, tools are important. Start with the basics: 5S, value stream mapping, and visual management. These are great for building momentum and getting quick wins. As your team gets more comfortable, you can introduce more advanced concepts like kanban and heijunka.
The key is to adapt these tools to your specific needs. I once worked with a hospital that used Kanban cards for managing medical supplies. It worked beautifully, but it looked nothing like what you’d see in a Toyota plant. Context is king.
Breaking Down Silos and Fostering Collaboration
In my experience, one of the biggest roadblocks to lean success is departmental silos. You know the drill: marketing doesn’t talk to sales, engineering is at war with production, and everyone blames IT when things go wrong.
Breaking down these silos isn’t easy, but it’s essential. Start by creating cross-functional teams for improvement projects. Get people out of their comfort zones and working with colleagues they normally wouldn’t interact with.
Visual management can be a massive hit and its a good idea to use. I’m a big fan of obeya rooms – war rooms where teams can come together to solve problems and track progress. It’s amazing how much easier collaboration becomes when everyone’s looking at the same data.
Measuring and Celebrating Progress
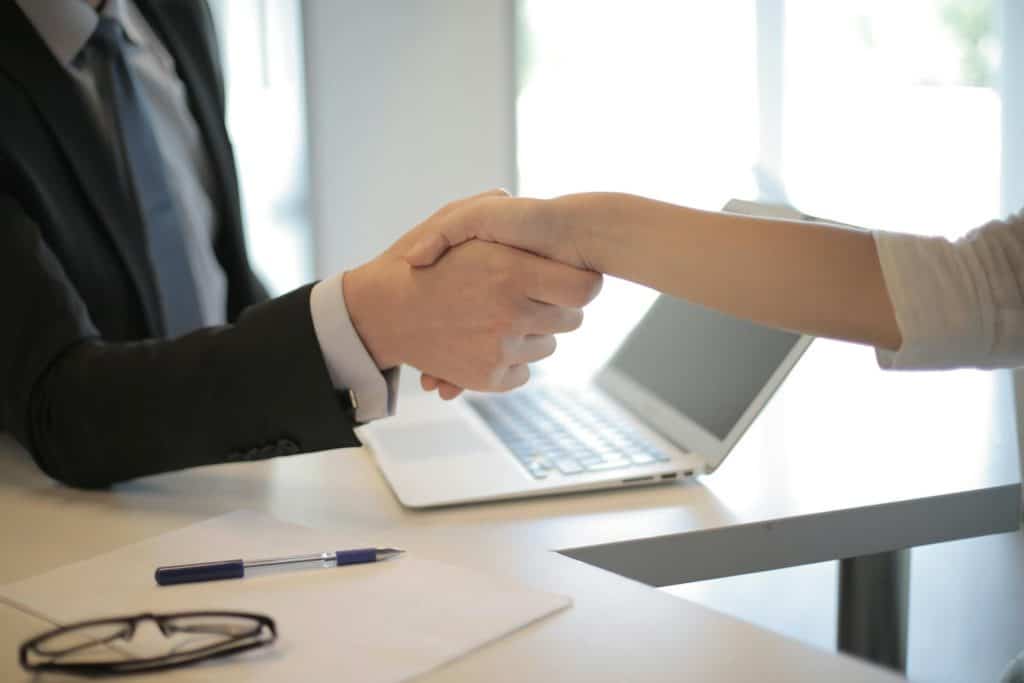
If you can’t measure it, you can’t improve it. But be careful – choose your metrics wisely. I’ve seen companies get so caught up in hitting arbitrary KPIs that they lose sight of the bigger picture.
Focus on metrics that truly matter to your business and your customers. Cycle time, first-pass yield, and customer satisfaction are usually good places to start. But don’t stop there. Encourage teams to develop their own metrics that are meaningful to their work.
And when you see improvement, celebrate it! Too often, companies move on to the next problem without acknowledging progress. A little recognition goes a long way in maintaining momentum.
Overcoming Common Obstacles and Resistance
Let’s face it: change is hard. You’re going to hit roadblocks. Middle managers often feel threatened by lean initiatives. Long-time employees may be sceptical. Resource constraints can derail your efforts.
The key is to anticipate these challenges and have strategies in place to address them. For middle managers, involve them in the planning process. Give them ownership over certain aspects of the transformation. For skeptical employees, use pilot projects to demonstrate success. As for resources, start small and use early wins to justify further investment.
Sustaining Lean Culture Long-Term
Here’s where the rubber meets the road. Implementing lean is one thing; sustaining it is another beast entirely. I’ve seen too many companies declare victory after a few months, only to slide back into old habits.
The key to sustainability is making lean part of your daily operations. It should be how you do business, not something extra you do. This means continual reinforcement of lean principles. It means evolving your approach as your organization grows and changes.
Leaders setting the standard is crucial here. When leaders make lean practices part of their routine, it sets the tone for the entire organization. And don’t forget about onboarding – make sure new hires are immersed in your lean culture from day one.
Lean Beyond Manufacturing: Applying Principles Across Industries
Now, I know what some of you are thinking: “This all sounds great for manufacturing, but I’m in a different industry.” Here’s the thing: lean principles can be applied anywhere there’s work to be done.
I’ve helped implement lean transformation in hospitals, software companies, and even educational institutions. The core principles remain the same, but the application looks different. In healthcare, it might be about reducing patient wait times. In software development, it could be streamlining the code review process.
The key is to focus on the underlying principles – identifying value, eliminating waste, and continuous improvement – rather than getting hung up on specific tools or terminologies.
Case Studies: Successful Lean Transformations
Let me leave you with a couple of real-world examples. I worked with a mid-sized electronics manufacturer that was struggling with quality issues and late deliveries. By implementing a pull system and focusing on built-in quality, they reduced defects by 20% and cut lead times in half within a year.
Another success story comes from a surprising place – a local planning office. By applying lean principles to their permit approval process, they reduced processing time from 15 days to just 5, while improving accuracy and customer satisfaction.
The common thread in these success stories? A full-blown approach that combined tools, culture change, and unwavering leadership commitment.
In conclusion, cultivating a lean culture is no small feat. It requires patience, persistence, and a willingness to challenge the status quo. But when done right, the results can be transformative. Remember, lean is a journey, not a destination. Keep pushing, keep improving, and most importantly, keep learning.