Lean tools can revolutionize your business processes. I’ve implemented these techniques in countless factories and seen remarkable results. Lean tools streamline operations, reduce waste and boost productivity. They’re not just for manufacturing. Service industries, healthcare and tech companies all benefit from lean principles. Let’s explore how these powerful tools can transform your business.
Overview of Lean Tools
Lean tools are methods designed to optimize processes, eliminate waste and boost efficiency. These processes originated in manufacturing, but today they exist in virtually any industry. The history of lean methodology dates back to the early 20th century in America. Henry Ford was one of the earliest innovators to use lean principles on the Model T assembly line. Then, Toyota took lean principles to the next level in the 1930s and developed Just-In-Time production as well as the Toyota Production System.
At its core, lean management is based on a set of principles:
- Define value from the customer’s perspective.
- Map the value stream.
- Create flow.
- Establish pull.
- Continuously improve.
By implementing lean tools, you’ll experience the following benefits:
- Lower operational costs
- Higher quality
- More engaged employees
- More satisfied customers
- Shorter time to market.
I personally have witnessed businesses completely turn around after implementing these lean tools. I’ve worked with everything from small startups to Fortune 500 companies, and the same lean principles always apply. Even if you don’t do any manufacturing, you can still use lean tools. The service industry, healthcare and even government organizations have used lean to see incredible results.
However, you might be wondering how the lean tools can apply to you. Let’s take a look at some of the key lean principles that will help optimize your processes.
5S: Workplace Organization
5S is one of the core lean methodologies and is designed to create an organized, efficient workspace. I’ve used 5S in various settings with excellent results each time.
The steps of 5S implementation are:
- Sort: Eliminate anything that isn’t necessary.
- Set in Order: Organize what’s left.
- Shine: Clean everything.
- Standardize: Document consistent processes.
- Sustain: Make it standard practice.
The benefits of 5S are outstanding. You’ll spend less time searching for tools and materials and see a significant improvement in safety. Morale commonly increases, and productivity improvements of 10-30% are standard.
One example that comes to mind is a small manufacturing plant. The workspace was a mess, with tools scattered everywhere and inventory all over the place. We implemented 5S, and within a few weeks, productivity was up 25%. The employees were also happier, and the plant manager was thrilled with the changes he saw as a result of our work.
5S isn’t exclusive to factory settings. It also works well in office environments, hospitals, schools, and beyond. Any workspace can implement this basic yet incredibly effective technique.
Kanban: Visual Management System
Kanban is a visual system for managing work. It originated from the factories of Toyota and is now applied to software development, project management and more.
At its core, a Kanban system consists of:
- Visual representation of work
- Work in progress limits
- Commitment to continuous flow
Kanban helps teams see their workflow, limits work in progress to avoid overload and promotes continuous flow of work items.
You can use Kanban to manage any process in a business:
- Software development
Marketing campaigns
Customer support tickets
HR onboarding - I’ve seen Kanban dramatically improve the efficiency of a disorganized business. For example, a tech startup I consulted with frequently completed projects behind schedule. We implemented a basic Kanban board, and suddenly the bottlenecks in their workflow became clear as day. The team was able to quickly identify and solve these problems. Project completion times dropped by 40%.
Kanban is a visual tool that anyone can understand. It fosters transparency and collaboration, and you’ll quickly realize that you can use it to manage any workflow of work items.
Value Stream Mapping
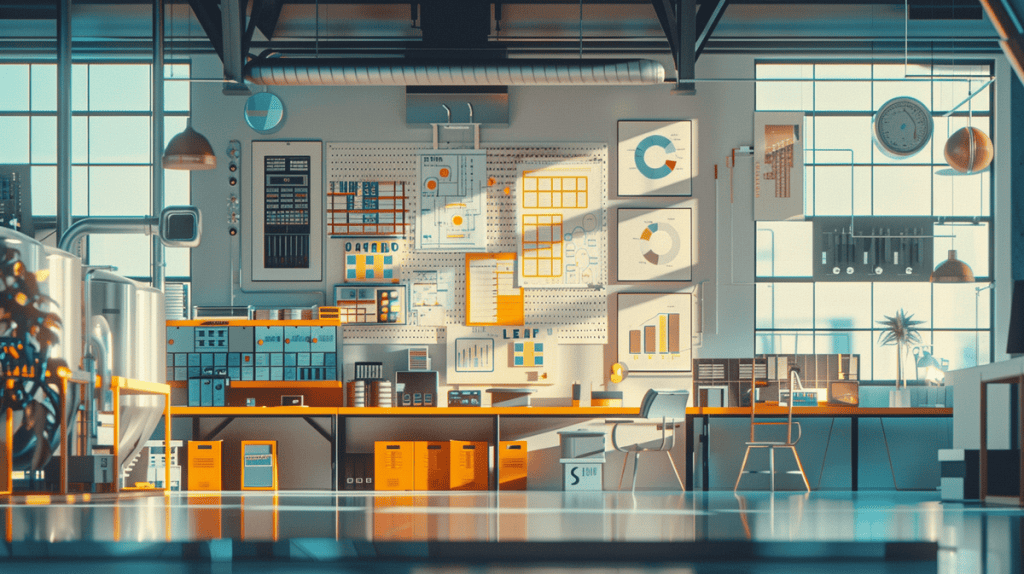
Value stream mapping (VSM) is a key lean tool. It’s a visual representation of how materials and information flow through a given process. VSM is designed to help you identify waste and improvement opportunities.
Here’s how to create a Value Stream Map:
- Choose a product family
- Draw the current state map
- Analyze the current state
- Create a future state map
- Implement the future state
VSM makes it very easy to see non-value added activities. It will show you where time and resources are being wasted in a process. As a result, you can make your processes much more efficient.
For example, I once worked with a large automotive supplier. Their production lead times were uncompetitive. After a VSM exercise, we learned that 80% of their lead time was waiting time that was non-value added to the customer. They redesigned their process, and they were ultimately able to reduce lead times by 60%.
VSM isn’t just for manufacturing companies. I’ve used it in a healthcare organization to improve patient flow. In a software team, it was also instrumental in reducing time to market. Any process with multiple steps can benefit from this tool.
Six Sigma: Data-Driven Quality Improvement
Six Sigma is a data-driven quality improvement methodology, designed to remove defects and achieve as close to perfect quality as possible. The name Six Sigma refers to the goal of producing a process that creates only 3.4 defects per million opportunities.
The DMAIC process is the overarching process used in Six Sigma:
- Define – Identify the problem and project goals
- Measure – Collect data on the current process
- Analyze – Identify the root causes of defects
- Improve – Implement the solution and verify the defects have been removed
- Control – Maintain the improved process
Six Sigma uses a wide array of statistical tools, including control charts, process capability analysis, and design of experiments.
It’s common in:
- Manufacturing
- Healthcare
- Financial Services
- Telecommunications
I’ve implemented Six Sigma projects in all these industries. One of the best projects I led was in a call center.
We used Six Sigma to reduce customer wait times by 70%. Not surprisingly, customer satisfaction scores improved dramatically. Plus, the company saw millions in operational cost savings.
The reason Six Sigma is so powerful comes down to its disciplined, data-driven approach to process improvement. It’s an excellent methodology when you have a complex process with a lot of data.
Just-In-Time (JIT) Production
JIT is a lean manufacturing approach to producing only what’s needed, when it’s needed, and in the quantity it’s needed. JIT reduces inventory costs and improves operational efficiency.
The advantages of JIT include:
- Lower inventory costs
- Better cash flow
- Ability to react more quickly to changes in the market
- Better quality control
- Higher overall productivity
The primary downside of JIT is the difficulty of execution. You must have extremely tight coordination with your suppliers. If the supply of raw materials is interrupted, you can’t produce anything. That said, the benefits of JIT often make the challenge worthwhile.
For example, one electronics manufacturer we worked with had serious issues with excessive inventory. We installed JIT, and its inventory carrying costs decreased by 40%. It also became far more responsive to changes in production demand.
Toyota is often cited as a success story of JIT implementation. Dell Computers is another excellent example, which used JIT to run a highly efficient build-to-order model. These are proof points for JIT’s effectiveness across various industries.
Kaizen: Continuous Improvement
Kaizen is a Japanese word that means “change for the better.” It’s a philosophy of continuous incremental improvement. Kaizen is for everyone, from the CEO to the frontline worker.
Implementing Kaizen in your organization:
- Encourage all employees to make suggestions for improvements.
- Create cross-functional teams for Kaizen events.
- Make small, achievable improvements.
- Implement improvements immediately.
- Measure and celebrate the success.
A kaizen events is a short and intense improvement project. These events typically last 3-5 days. During an event, a team will analyze a process, identify waste, and make improvements.
I’ve led countless Kaizen events. One of the most memorable took place in a hospital. We worked to reduce patient discharge times. During the event, the team identified several improvements to make. Within a week, we had reduced discharge times by 30%.
It’s critical to measure the impact of the improvements from Kaizen events. Capture some key performance indicators before and after the improvement. You’ll often see massive results from seemingly small improvements.
SMED: Single Minute Exchange of Die
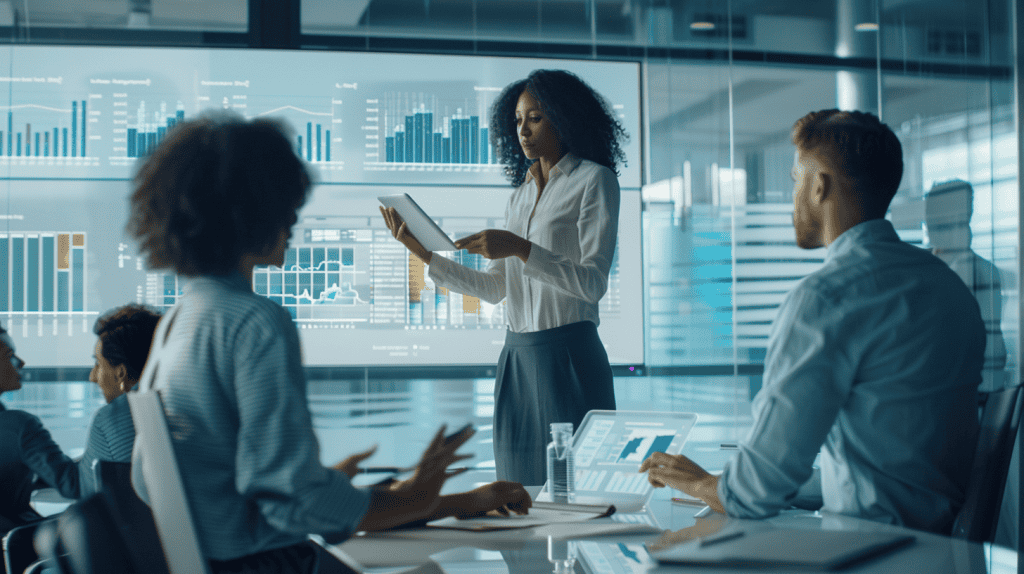
SMED is a lean tool to reduce equipment setup time, and the goal is to achieve setup times in less than 10 minutes. This is essential for flexible manufacturing.
Steps to implement SMED:
- Observe the current setup process.
- Identify internal versus external activities during setup.
- Change the internal activities to external whenever possible.
- Simplify the remaining activities.
- Standardize and document the new setup process.
SMED has several benefits. It reduces the time between setup and production runs, which maximizes machine utilization and output. This allows you to produce smaller lot sizes and maintain less inventory.
I have implemented SMED across various industries. One company that machined automotive parts had painfully long setup times. We went through the SMED principles, and setup times went from nearly two hours to 15 minutes. As a result, this company’s production capacity went up by 25%.
SMED is most applicable in industries with frequent setups, like automotive, electronics, and food. However, you can apply the same principles to any setup process.
Jidoka: Built-in Quality
Jidoka is a lean concept that emphasizes built-in quality. it allows machines and operators to identify an abnormality and stop production. This prevents defects from occurring within the system.
How to implement Jidoka in production processes:
Design of the process an error can stop.
Install an automatic stop.
Train operators to notice an error and stop.
Teach operators to solve the problem immediately.
Regularly work on improving jigoku.
Jidoka will immediately eliminate defects and rework. You will achieve a step-change in quality. Operators love it and feel they have more control over quality.
I’ve implemented Jidoka in quality control processes in many companies. One electronics manufacturer had astronomical defect rates. We implemented Jidoka. Defect rates decreased 80%. We also saved production time, as people no longer had to inspect and rework.
You can use Jidoka in any process where you need quality as a requirement. For example, software companies use Jidoka for automated testing. Service businesses use it for customer interaction processes. If you have a process where quality really matters, you can introduce Jidoka principles.
Lean tools are powerful allies in your quest for improvement. From 5S to Jidoka, each technique offers unique ways to streamline processes and boost efficiency. I’ve seen these tools transform struggling facilities into powerhouses of productivity. Remember, success lies in consistent application and adaptation to your specific needs. Start small, measure results, and scale what works. Your journey to excellence begins now.