Cellular manufacturing is a more efficient way of organizing workstations in a logical order. With a cellular layout, you organize workstations in the sequence that makes the most sense for the product being manufactured.
This significantly increases efficiency, minimizes waste, and improves product quality. I’ve used cellular layouts in several different industries with great success. In this course, you’ll learn how this layout can completely change your operations, simplify workflows, and increase productivity more than you thought possible.
Definition and Principles
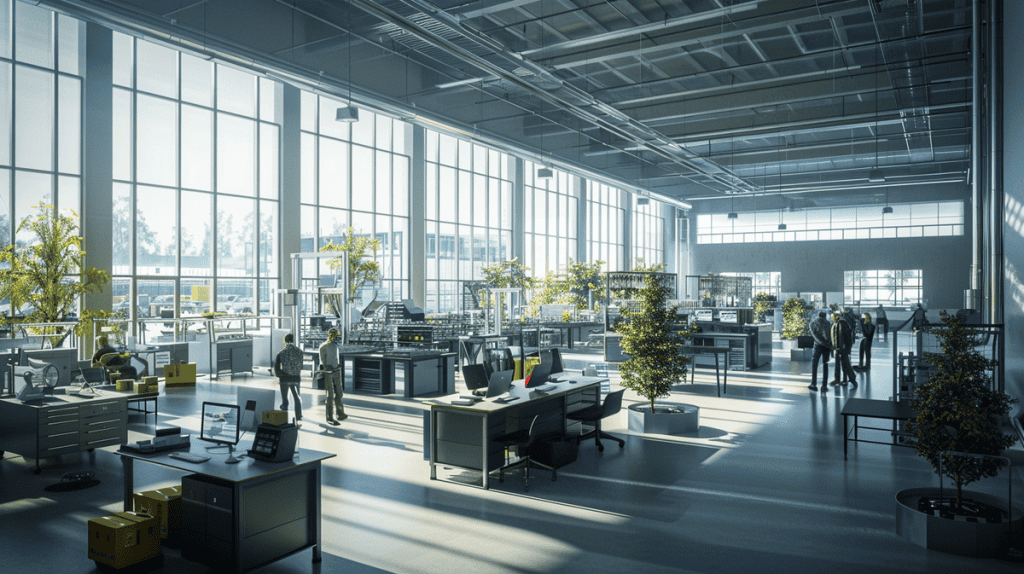
Cellular manufacturing organizes production workstations and equipment in a sequence to facilitate smooth material and component flow. It groups similar products together and locates the equipment close together. The layout is optimized for flow. It’s closely related to lean manufacturing and just-in-time manufacturing.
I’ve witnessed this layout change entire factories. When I started my career working on a production line, the factory was a disaster of inefficiency. Once we switched to cellular manufacturing, it was like a lightbulb went off. Suddenly, parts were flowing smoothly from one station to the next. Workers could talk to each other and solve problems as they arose.
The concept is deceptively simple and incredibly impactful. You essentially build mini manufacturing units called “cells.” Each cell produces a family of closely related products. This limits unnecessary transportation and waiting.
The entire focus of cellular manufacturing is maximizing flow and eliminating waste. You’ll see waste disappear in almost every form. No more excess inventory piling up. No more 100-yard walks between work stations. It should all be right there in the cell.
And as a manager or engineer, this means faster manufacturing lead times and better quality control. You can catch quality issues early and continuously improve the process. It’s a great feedback loop.
Lean Startup is often used in conjunction with cellular manufacturing. Both are designed to maximize value and minimize waste.
Cellular Layout Types
Cellular manufacturing layouts come in different forms, each with its own set of benefits.
U-shaped cells are a favorite because they are:
- Easy to supervise
- Easily scale staffing
- Encourage good operator communication
Straight line cells work well for basic processes that go in a straight line.
L-shaped and T-shaped cells are great solutions if you have an awkward factory layout.
O-shaped (cage) cells offer operators full access to the product from all sides. This is great for assembly type processes.
S-shaped cells help you fit a lot of production steps into a small area.
Selecting the best layout comes down to your unique situation. Consider your product, layout and process. I’ve helped companies identify layouts that increased their productivity by 50% or more.
Keep in mind the best layout may change as you grow and scale your production.
Benefits of Cellular Manufacturing
I’ve personally witnessed the power of cellular manufacturing in various industries. The advantages are compelling and diverse.
Higher productivity and efficiency:
- Less material movement
- Less transit time
- Faster changeover between products
Lead times can drop by an order of magnitude. WIP inventory often falls by 50% or more. Quality is higher as any defects are caught and fixed inside the cell.
Your operations will also be more adaptable. It’s much easier to react to changes in demand. Cells can be reconfigured much more quickly than a traditional production line.
The cost savings are significant. You’ll use less floor space, improving your labor efficiency. Labor and equipment productivity both increase.
Employee morale often skyrockets. By creating a cell, workers feel a sense of ownership. They also directly see the results of their work.
The results speak for themselves. 43-53% of companies in the US and UK use cellular manufacturing. As you look at larger companies (those with 100+ employees), the rate is 73%. These companies have recognized the advantage of cellular manufacturing.
In my consulting work, I’ve seen companies double or triple their production capacity through cellular manufacturing. The potential improvement is massive.
Implementing Cellular Manufacturing
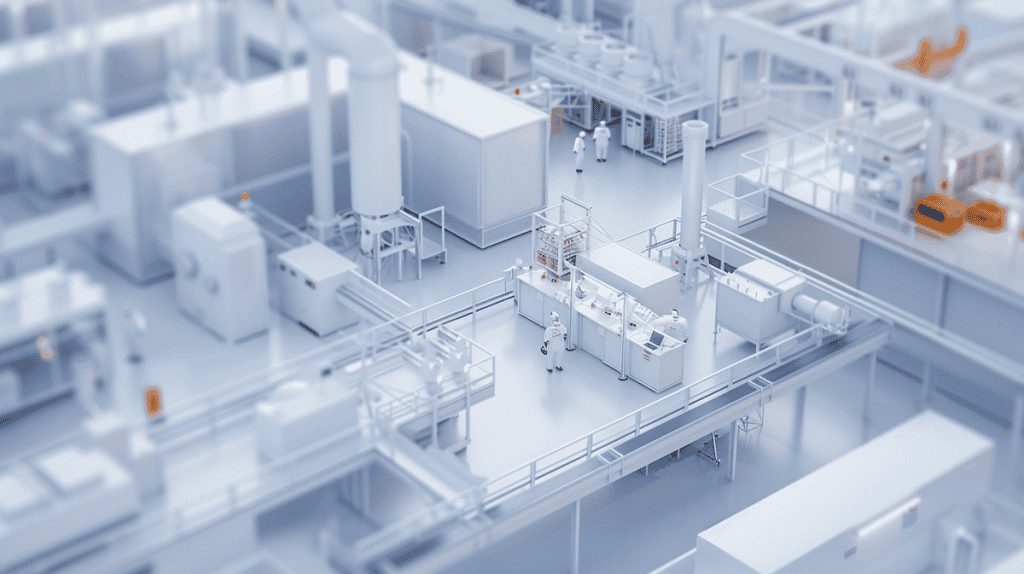
Switching to a cellular layout takes thoughtful planning. Here’s a simple process to get started:
- Product Mix Analysis
- Product Family Identification
- Equipment and Workstation Grouping
- Cell Layout Design
- Employee Training
- Implementation
- Ongoing Monitoring and Adjustment
Begin by deeply understanding your products and processes. Then, group products into families and design your cells around them.
Next, consider which equipment and workstations each product family requires and design a logical cell sequence based on it.
Designing the layout is a challenge. Consider material flow and worker motions and communication requirements. Test different configurations before finalizing.
Training is essential for employees. Ensure they understand the new system and their role within it. Stress the role of teamwork and how you expect them to always be improving what they do.
Implement the change step by step. Do a small pilot cell first. Learn. Then, expand to your larger operation.
After it’s implemented, watch the performance to see if it meets your expectations. Be prepared to adjust. Continuous improvement is why we establish cells in the first place.
Team Dynamics in Cellular Manufacturing
Cellular manufacturing encourages a more empowered, collaborative team.
Teams in cellular manufacturing are self-directed teams with no more than about 8-12 people.
They have become cross-functional teams in that they don’t have a direct leader.
Cross-functional teams encourage cross training. That means everyone in the cell does more than one job. This makes the team more flexible, happier and ensures the team can always operate – even if someone is missing.
Communication is a lot smoother in a cell. Everyone is located close together and can easily talk about problems and solutions. And you can solve problems at the source quickly.
The role of leadership changes quite a bit. The leader is no longer doing direct leadership. Instead, he or she provides resources and training the team needs to be effective.
Increased employee empowerment. They say the team members should make 99% of the decisions. This allows the teams to solve problems faster and have more pride.
Teams establish great conflict resolution skills. Inside the best-practice companies, it’s only the teams that are doing the work to resolve problems.
Historical Development of Cellular
Cellular manufacturing has a long history. It originated from group technology, which was first presented by Ralph Flanders in 1925.
Sergei Mitrofanov then introduced these ideas to manufacturing processes as early as 1933 in Russia. This laid the foundation for cellular manufacturing as we know it today.
In the 1970s, Japanese companies started to incorporate cellular manufacturing with their lean production practices, and it was highly successful.
In the 1980s, the concept made its way to the U.S. as part of the just-in-time production movement, and American companies quickly adopted cellular manufacturing after realizing its benefits.
Today, cellular manufacturing has become widespread globally. It has also been slightly modified and applied to various industries. While the fundamental principles of cellular manufacturing are the same, it’s now used in a wider variety of ways.
Now, cellular manufacturing is a key component of modern production systems, and it continues to adapt as new management practices and technologies emerge.
Challenges and Limitations of Cellular
While cellular manufacturing is a powerful solution, it’s not without its challenges.
The initial investment can be significant. Reorganizing your factory layout and retraining workers requires both time and money. Some businesses find it difficult to justify this investment upfront.
Resistance to change is a common challenge. Workers who have done things a certain way for years might be resistant to change, and management might be hesitant to disrupt the existing operation.
Balancing the workload of each cell can be a challenge. If you don’t do this correctly, some cells will become bottlenecks while others have excess capacity.
Product mix changes can be problematic. If you design cells for specific product families, and something changes in your demand plan, it can create problems.
High variety and low volume manufacturing can complicate the situation. You need to be very flexible, yet you also want the benefits of cells, which requires a delicate balance.
Redundant equipment is another potential downside. If you build a similar cell elsewhere, you may have duplicate machines, which drives up your capital investment.
However, I’ve seen companies successfully address all of these challenges with good planning and execution. And the benefits of cellular manufacturing often significantly outweigh any of these drawbacks.
Closing out
Cellular manufacturing is transforming manufacturing operations, increasing efficiency and quality and reducing costs and lead times. I’ve witnessed the impact of cellular manufacturing in several different industries.
Teams operate more effectively within this model and learn new skills and take more pride in their work. However, it’s not all rainbows and sunshine. Setting up a cellular layout requires detailed planning and change management.
Yet the payoff is significant. Companies that figure out cellular manufacturing have a distinct advantage in today’s market.