Industry 4.0 is changing manufacturing through the use of smart technologies. Real industry 4.0 examples illustrate how it improves efficiency, productivity, and innovation. I’ll discuss how businesses apply IoT sensors, AI, robotics, and digital twins to reinvent their processes.
You’ll learn how these smart technologies increase throughput, minimize downtime, and optimize supply chains. So, let’s look at specific examples that reveal how you can use Industry 4.0 today.
Industry 4.0 Examples in Manufacturing
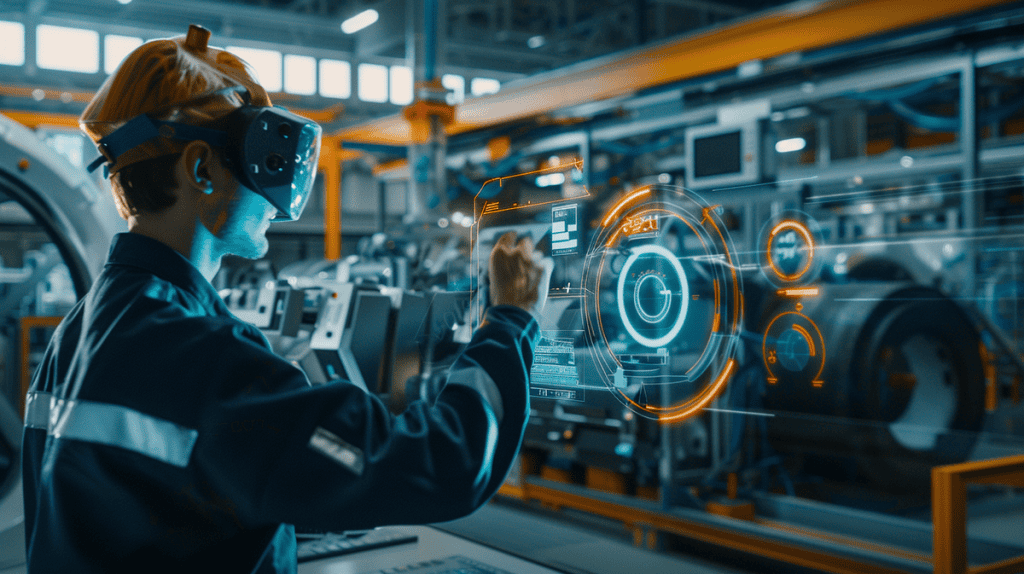
Industry 4.0 technologies are revolutionizing manufacturing. Here are the key technologies:
Smart sensors and IoT devices: Smart sensors and IoT devices gather real-time data from machines and processes, allowing for continuous monitoring and quick decision-making.
Cloud computing and data analytics: Cloud platforms store and process massive amounts of data, and data analytics tools extract insights to optimize operational processes. According to IDC, manufacturers will spend $9.2 billion on cloud platforms in 2021.
AI and ML: AI and ML algorithms analyze data to optimize processes, automate decisions, and predict when machines need maintenance.
Additive manufacturing (3D printing): Additive manufacturing, also known as 3D printing, can produce complex parts with minimal waste. It’s primarily used for prototyping and small-scale production runs.
AR and VR: AR and VR help with training, maintenance, and product design. They also deliver immersive experiences for workers.
Robotics and automation: Through robotics and automation, more advanced robots and automated systems can handle various repetitive tasks, ultimately boosting efficiency and precision in manufacturing processes.
These technologies all contribute to making factories smarter and more efficient. They’re the foundational technologies of Industry 4.0.
Smart Factories: Real-World Applications
Smart factories are no longer just a theoretical idea as there are now real-world examples of them. For instance:
Bosch has a connected smart factory in Wuxi, China that’s making a significant impact. Through the use of sensors and advanced analytics, the factory has seen productivity increase by 10% in some areas.
Siemens has the Amberg Electronics Plant, which is one of the most automated factories in the world. Machines and computers complete 75% of the value chain without any human involvement. As a result, the factory has achieved a defect rate of less than 12 parts per million.
The Tesla Gigafactory is one of the most advanced examples of a smart factory. It relies on advanced robotics and artificial intelligence to produce electric vehicles and battery packs. The factory is specifically designed to be the most advanced car factory in the world and has a goal of reducing production costs by 30%.
These factories are living proof that Industry 4.0 technologies can revolutionize manufacturing. They’re generating more output with the same level of input, achieving better quality and reducing total cost.
Robotics and Automation in Industry 4.0
Robots are transforming manufacturing:
- Collaborative robots (cobots) on assembly lines: Cobots are robots designed to work alongside humans. They perform the repetitive work while humans handle the more complex tasks. This collaboration ensures that work gets done faster and without strain on the humans.
- Autonomous Mobile Robots (AMRs) in warehouses: AMRs are robots that navigate a warehouse without human intervention. They move materials around and fulfill orders. By implementing Fetch Robotics’ AMRs, companies can decrease an order’s cycle time by 50% and double picking productivity.
- Automated Guided Vehicles (AGVs) in logistics: AGVs are robots that move materials around factories. They follow predetermined routes and are a key part of an efficient material flow, all with zero labor expense.
- Quality control robots in manufacturing: Robots are often better than humans at very precise tasks. By using sophisticated sensors and AI, these robots can inspect products for defects. They’re more accurate than human eyes and can therefore produce a higher quality product.
Robotics and automation are the backbone of Industry 4.0. They’re implementing smarter, more efficient, and more competitive factories.
Digital Twins in Industrial Applications
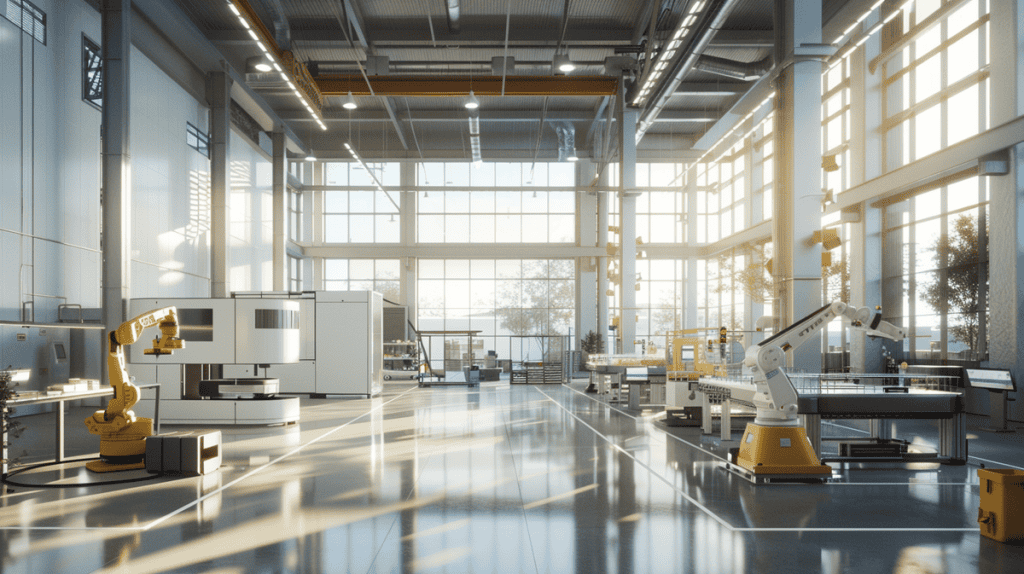
Digital twins are virtual representations of physical objects or processes, and they’re playing a key role in Industry 4.0. In fact, Gartner estimates that by next year, 50% of all large industrial companies will leverage digital twins.
GE is a great case study of digital twins in action. They use digital twins to optimize jet engine maintenance. For each jet engine, they create a digital replica of the engine. Within the digital twin of the engine, they simulate its performance and predict its maintenance schedule. As a result, their engines are more reliable, and they experience less downtime.
Siemens does something similar with digital twins and wind turbines. Today, they digitally model entire wind farms to optimize each turbine’s placement and predict its energy output. This allows them to produce more energy with each wind farm and ensure the turbines require less maintenance.
The main advantage of digital twins within predictive maintenance is that they predict when a piece of equipment will fail. After engineering a digital twin of a piece of equipment, engineers can simulate how and when it will fail. As a result, they can optimize when they perform maintenance to avoid unnecessary downtime, implementing changes to structures or machinery, and more.
IoT and Predictive Maintenance
Here are a few real-world examples of IoT and predictive maintenance:
Rolls-Royce has an IoT engine health monitoring system that integrates IoT sensors into the company’s aircraft engines. These sensors collect data about the performance of the engine, and the system uses this data to predict when the engine will require maintenance. This strategy has significantly reduced the amount of unplanned maintenance, and it has made the engines more reliable.
Caterpillar has Cat Connect, an IoT solution for construction and mining equipment. It tracks machine health and fuel consumption, as well as operator behavior. With this information, customers can optimize their operations and reduce the risk of the machine breaking down.
Konecranes developed the TRUCONNECT remote monitoring system, an IoT solution for cranes and lift trucks. It tracks condition parameters and usage patterns, allowing Konecranes to predict when a machine will require maintenance and make the machines safer to operate.
Airbus implemented IoT for aircraft maintenance. The company has equipped its planes with sensors that monitor the performance of different systems on the plane. The company then uses this information as data to predict when the plane will need maintenance.
These examples demonstrate how IoT and predictive maintenance are making businesses more efficient and lowering costs.
Big Data and Analytics in Supply Chain Management
Big data is revolutionizing supply chain management, and it can reduce forecast error in demand forecasts by at least 85%. Here’s a look at how some businesses are leveraging big data:
Amazon has an anticipatory shipping model, fueled by big data analytics, through which it predicts what customers will buy and ships the items to local distribution centers before customers actually place orders. As a result, Amazon can deliver products to customers even faster, which positively impacts customer satisfaction.
Walmart uses big data analytics to optimize its supply chain. The company combines big data, including historical sales data, weather data, and social media trends to predict demand and ensure each store has the right inventory levels of each product. The benefit is less waste and better inventory management.
Procter & Gamble has a consumer-driven supply network and uses big data to analyze consumer behavior through POS data, social media data, and economic data. It can then adjust production and distribution to better meet consumer demand. The result is a more demand-driven supply chain.
These are just a few Industry 4.0 Examples, but they illustrate how big data can ultimately make a more efficient supply chain that’s better aligned with what consumers actually want.
Human-Robot Collaboration in Manufacturing
Human-robot collaboration is one of the main themes of Industry 4.0. MIT found human-robot collaboration can reduce idle time for workers by 85%. Here are a few examples of how companies are implementing human-robot collaboration:
BMW has implemented collaborative robots in its assembly lines. These robots help human workers, performing tasks that are too heavy or too repetitive. As a result, the robots take much of the physical strain off of human workers, making the tasks more ergonomic. The outcome is the workers are more productive and have better working conditions.
Audi uses a robotic assistant called PART4you that collaborates with humans in logistics. The robot picks up items and hands them to other humans in the assembly line. Through doing so, it is able to prevent the human workers from bending down or reaching up repetitively. The result is greater efficiency and less physical stress on the workers.
Universal Robots offers collaborative robot solutions for various industries. The key to Universal Robots’ success is its cobot, which a non-expert can program. The key to the cobot is it can easily be re-deployed on a different task. As a result, small and medium manufacturers can cost-effectively implement automation.
Each of these examples demonstrates how human-robot collaboration can make manufacturing more efficient while also improving working conditions for humans.
Finishing off
Industry 4.0 technologies are transforming manufacturing as we know it. Smart sensors, digital twins, and other advancements optimize efficiency and productivity in the factory. These technologies aren’t just theoretical, either. Bosch’s connected factory, for instance, boosted production by 10%.
Robotics and automation are making operations more efficient, and AMRs have cut order cycle times in half. Thanks to IoT, predictive maintenance is reducing costs and downtime.
Supply chain management has also benefited from big data analytics, and demand forecasts are up 85%. Human-robot collaboration has also slashed worker idle time by 85%. This is a truly transformational time in manufacturing, and if you implement these Industry 4.0 Examples , you’ll keep your company ahead of the competition.