Lean construction revolutionizes project management. I’ve seen it transform chaotic jobsites into efficient machines. You’re about to discover how this approach can slash waste, boost productivity and improve your bottom line. Lean principles apply to projects of all sizes from renovations to skyscrapers. Let’s explore how lean construction can take your projects to the next level.
What Is Lean Construction?
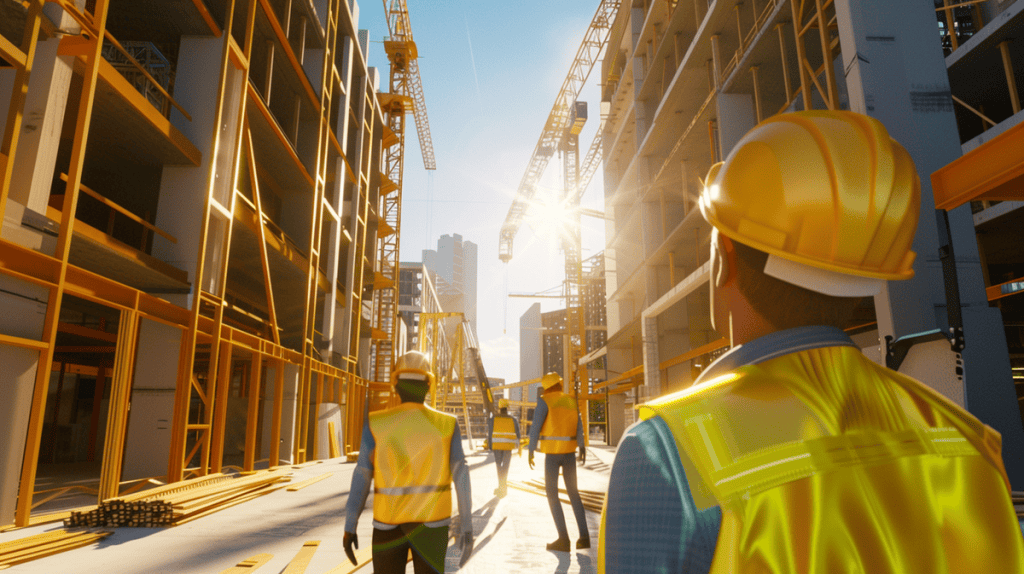
Lean construction is a powerful way to manage projects in the construction industry, and I’ve seen it transform operations as a consultant. At its core, lean construction aims to minimize waste and maximize value. It’s based on manufacturing principles and tailored to construction’s specific challenges.
At a high level, lean construction principles are all about optimizing efficiency and collaboration. This means continuous flow, pull planning, and just in time. These differ significantly from traditional construction principles, which optimize value through value stream mapping, the last planner system, and integrated project delivery.
Implementing lean construction delivers a multitude of benefits. You’ll reduce costs, increase quality, and deliver your projects more quickly. Safety tends to improve, too. Team structures become more engaged and enjoy working more as a team. End clients are more satisfied with the results.
Essentially, lean construction is about “designing production systems to minimize waste of materials, time, and effort so that value can be maximized” (Koskela et al. 2002). This confines the whole point of adopting lean principles.
In my experience with dozens of construction firms, those that adopted lean principles almost always saw dramatic transformations. Projects ran more smoothly, and they solved problems more quickly. Everyone, from laborers up to project managers, felt more engaged with the end results.
Key Tools and Techniques of Lean Construction
There are several key tools and techniques within lean construction. Each tool has a specific purpose to eliminate waste and streamline processes. Here’s an overview of the primary methodologies you’ll encounter:
- Last Planner System (LPS):A collaborative scheduling method Improves workflow predictability Enhances accountability within the team
- Pull Planning: A reverse method of scheduling Ensures tasks are completed just in time Reduces waiting and inventory waste
- Value Stream Mapping (VSM): Allows you to see the entire process of a project
Identifies waste and inefficiency Helps you understand what to improve - 5S Workplace Organization: A strategy to organize any work area Reducing waste of motion (e.g., looking for tools) Improving safety and productivity
- Kaizen (Continuous Improvement): Encouraging small, gradual changes Empowering team members to make changes Creating a culture of continuous improvement
These techniques are the foundation of lean construction. I’ve used these techniques on various construction projects with amazing success. The foundation of many essential lean construction ideas dates back to Henry Ford and his integration of the assembly line in the early 1900s.
Implementing Lean Construction Practices
Implementing lean construction is a systematic process. I’ve outlined the steps based on my experience coaching companies through the process:
- Assess existing processes
- Identify waste
- Plan implementation
- Train the team
- Establish metrics for success
- Control and adjust
You can start by assessing your current processes and pain points. Your team likely has plenty of ideas on where things are breaking down and can get a buy-in from them.
When planning implementation, consider what things might get in the way and which people are responsible for what. Then, make sure you allocate resources for training on lean principles. If you don’t, people won’t follow them. They also won’t work.
You also need to make sure you’re tracking metrics because if you aren’t measuring anything, you can’t control anything.
The biggest problem you’ll face is people not wanting to change. You can combat this by articulating the benefits of lean construction and getting small wins to build momentum.
Waste Reduction in Lean Construction
The primary goal of lean construction is waste reduction, and you can only reduce waste by understanding the types of waste you’re dealing with. In construction, the most common forms of waste include:
- Overproduction
- Waiting
- Transporting
- Over-processing
- Inventory
- Motion
- Defects
You identify waste by closely observing and analyzing. Walk through your project sites, talk to your workers, and look for any bottlenecks in the process or materials that seem to pile up in one spot. Technology is increasingly helpful here, as drones and sensors can track material flow and identify inefficiencies.
I’ve seen companies make a real impact on the bottom line by focusing specifically on eliminating waste. For example, one reduced material waste from over-ordering by 30% from simply managing it properly. Another reduced the overall timeline for every project by 20% by optimizing worker motion on site.
Here’s how the traditional way of thinking about waste reduction compares to a lean way of thinking about waste reduction:
Traditional Approach | Lean Approach |
---|---|
Reactive | Proactive |
Focuses on visible waste | Also fixes hidden waste |
Individual’s responsibility | Everyone’s responsibility |
Fixed process | Continual improvement |
. |
Ballard and Howell noted in 1994 that typically, only 50% of tasks on a weekly work plan are completed by the end of the planned week. Be sure to use Lean methods to get this percentage as close to 100% as possible
Improving Project Planning and Scheduling
Effective planning and scheduling are essential in lean construction. Collaborative planning techniques involve all stakeholders early in the planning process, reducing conflicts and ensuring everyone is aligned on project goals.
Just-in-time delivery helps minimize on-site material inventory. It’s a strategy to have materials on-site only when they’re needed, which reduces material storage costs and potential damage. Variability reduction strategies aim to standardize processes where possible.
Risk management in lean construction is about identifying risks early and addressing them during team meetings. These can help ensure a challenge doesn’t evolve into a significant issue.
Combining lean construction principles with project management software is a way to make sure everyone is in sync. Project management software tools can help track progress, allocate resources, and streamline communication across team members.
Key lean project planning best practices are:
- Use pull planning for detailed scheduling.
- Host daily huddles to identify key issues and course correct quickly.
- Utilize visual management boards to make information easily accessible.
- Cross-functional collaboration ensures teams work together effectively.
- Regularly review and update plans to continue improving project operations.
The Construction Management Association of America’s (CMAA) 2006 survey saw construction industry members voice gripes about inefficient work methods and the costs of waste in construction projects. Lean planning solves both of these problems.
Lean Construction and Building Information Modeling (BIM)
Lean construction and BIM are a match made in heaven. BIM improves visualization and coordination, which supports lean’s goal of maximizing efficiency and minimizing waste.
Applying BIM to lean processes is particularly helpful for improving clash detection, minimizing rework, and reducing material waste. The ability to virtually model projects is also helpful for planning and sequencing work, which is aligned with lean’s just-in-time delivery philosophy.
The main challenges of integrating lean and BIM are the initial investment and training resources. However, the long-term benefits far outweigh these initial costs.
Benefits of integrating lean and BIM include:
- Better project visualization
- Improved collaboration
- More accurate cost estimates
- Less rework
- More efficient facility management after the build
Looking ahead, there will be a closer marriage of lean principles and BIM technology. Currently, we’re seeing advancements in 4D and 5D BIM, which includes the time and cost dimensions.
Bertelsen (2003) also suggested that we should model construction through the lens of chaos and complex systems theory, meaning you can think of construction as:
1) A project-oriented production system,
2) An industry with autonomous agents, or
3) A social system. This is easily related to the holistic approach of integrating lean and BIM.
How to Measure Lean Construction Success
Measuring performance is critical in lean construction. Key Performance Indicators (KPIs) help track progress and determine where you can improve. Common KPIs include:
KPI | Description |
---|---|
Percent Plan Complete (PPC) | How much of your weekly work plans does your team complete? |
Cycle Time | How long it takes to complete a specific task |
First Time Quality (FTQ) | How often it’s done right the first time |
Safety Incidents | How many accidents or near-misses occur |
Cost Variance | The variance between what a task was supposed to cost and what it actually cost |
There are both simple and advanced options for tracking these KPIs. Some teams use basic spreadsheets, while others use advanced software platforms. The key is tracking them consistently.
Using these data points to make decisions is what drives continuous improvement. By regularly reviewing them, look for any trends or opportunities to make them better. It’s also important to include your team in this process, as they likely have insights into why you’re seeing certain data points.
In my consulting business, I’ve worked with a number of firms that have completely transformed their business simply by being more diligent about tracking KPIs. One client, for example, reduced the length of their projects by 25% after they started tracking KPIs rigorously.
Lean construction transforms the building industry. It slashes waste, boosts efficiency and delivers superior value. I’ve seen projects finish faster, safer and with higher quality using these methods. You now have the tools to revolutionize your construction processes. Remember, lean is a journey of continuous improvement. Start small, measure results and keep refining. With commitment and persistence, you’ll achieve dramatic gains in productivity and profitability. The future of construction is lean. Are you ready to lead the way?