Takt time(TT) is a crucial concept in production management. It’s the heartbeat of your manufacturing process, setting the pace for smooth operations. I’ve seen countless factories transform their efficiency by mastering takt time. You’ll learn how this simple yet powerful tool can revolutionize your production flow and boost your bottom line.
What Is Takt Time?
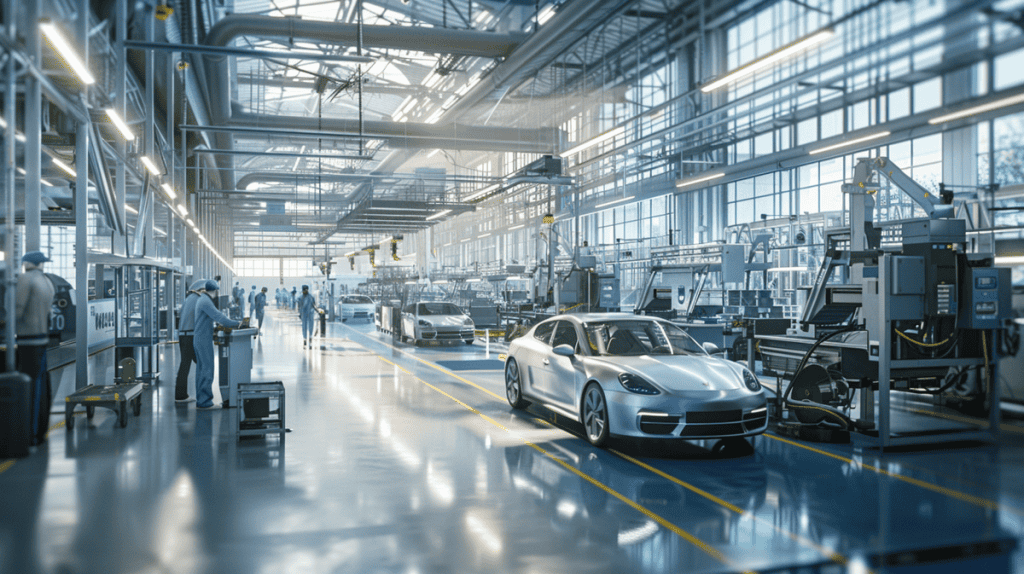
Takt time is one of the key concepts in lean manufacturing. It represents the rate at which products must be produced to satisfy customer demand. The term originates from the German word “takt,” which means rhythm or beat.
Takt time is deeply rooted in the history of efficiency:
- German aircraft industry in the 1930s
- Adoption by Toyota in the 1950s
- Widespread adoption in Toyota’s supply base by the late 1960s
- Popularization in lean manufacturing books in the 1990s
I’ve witnessed it dramatically transform production lines. It’s the heartbeat of lean manufacturing. It ensures production aligns with customer demand. This minimizes overproduction, which reduces waste.
In my experience working with a wide range of industries, it’s one of the best changes you can make. Specifically, it ensures a steady, predictable flow in production. Additionally, you simply can’t optimize resources effectively and deliver what customers need unless you use takt time.
Its also not just a metric. It’s a potent continuous improvement tool. When you truly understand and use takt time, you take a major step toward lean manufacturing excellence.
How to Calculate
The formula is simple: Available working time ÷ Customer demand. This is the ideal speed the production line operates under.
There are several things to consider when calculating:
- Customer demand
- Available working time
- Planned downtime
- Standard vs. heuristic
- Number of shifts
Here’s a step-by-step process to calculate:
- Identify customer demand
- Determine available working time
- Subtract planned downtime
- Divide working time by customer demand
Here’s an example:
Let’s say you’re running a bakery and your customers have demanded 480 loaves of bread per day. If you work 8 hours (480 minutes), and your lunch break is 30 minutes.
You have:
Available time: 480 – 30 = 450 minutes
Takt time: 450 ÷ 480 = 0.9375 minutes or 56.25 seconds
So, you should produce one loaf of bread every 56.25 seconds to produce enough to meet customer demand.
I’ve done this calculation in my consulting business more times than I can count and is a reason it is so valuable. It’s a powerful way to align production with customer demand, which is a critical value-adding activity. It’s also a something you can use as a tool to optimize processes and reduce waste.
Takt Time in Manufacturing
TT is the maestro of your manufacturing symphony. It dictates the cadence of your entire operation. When properly applied, it creates a seamless, melodious flow.
In my experience as a lean consultant, I’ve seen it turn disorderly manufacturing lines into paragons of efficiency. It’s the secret to balancing manufacturing lines. Each workstation operates at the same cadence, which prevents bottlenecks and overproduction.
Takt time is closely related to, but distinct from, cycle time. Cycle time is the amount of time it takes to complete a task. For best results, your cycle times should be a little less than takt time. This allows some flexibility in the manufacturing line.
In just-in-time manufacturing, TT is everything. It ensures you’re producing only what’s necessary when it’s necessary. As a result, it reduces inventory holding costs and frees up cash.
The benefits of applying takt time are as follows:
- Increased manufacturing productivity
- Less waste
- Improved manufacturing quality control
- Higher manufacturing customer satisfaction
- Happier manufacturing employees
I’ve seen these benefits in action across countless industries. When you align a manufacturing line with takt time, you set yourself up for success.
Implementing Takt Time
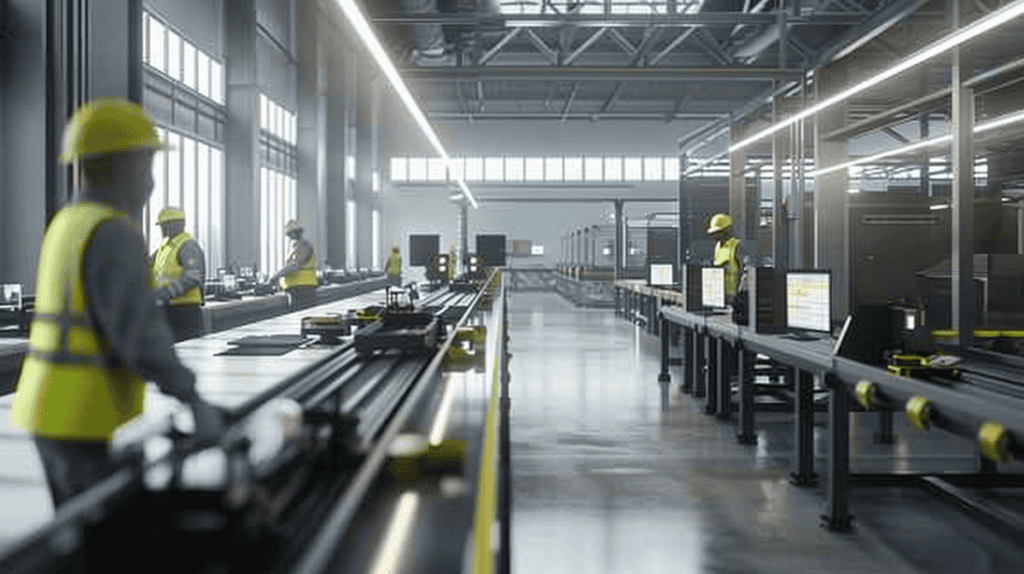
Introducing it into your production system is no small feat. I’ve walked many companies through this process, so I speak from experience when I say it’s difficult but very rewarding.
The first step is to analyze your current production flow, identify bottlenecks or other inefficiencies, and then establish your takt time based on customer demand. Then ensure your workstations can keep up with this pace.
Once its is in place, it’s critical to monitor it. This is where visual management solutions such as takt boards and digital displays come into play. These tools provide real-time feedback to operators, and I’ve found this instant feedback to be very helpful to help them ensure they’re running takt time.
Common Challenges
The most common challenges you’ll face when implementing:
- People who don’t want to change
- A forecast of customer demand that isn’t actually correct
- Equipment is not reliable enough
- Various operators are not all capable of working at takt time
To mitigate these challenges, focus on communication and training. Communicate the importance of takt time to the team, and ensure equipment is capable of reliable performance and cross-train operators to each be capable of working at takt time.
The best way to ensure its adhered to and actually effective is to:
- Start with a smaller pilot inside your operation
- Allow as many employees as possible to provide input
- Continuously check and adjust
- Do something nice for the team if they meet the goal!
Finally, recognize that implementing is never really done. Things will always come up that allow people or equipment to not work. Be patient and relentless about addressing these issues, and over time, you’ll see the production system work at takt time more often.
Takt Time and Continuous Improvement
Takt time is a great indicator of waste. If a station can’t meet its target, you know you have a problem that requires improvement. This visibility is why its so useful for any continuous improvement effort.
I’ve personally used it to drive process improvements across a variety of industries. It gives you a clear goal to optimize towards. Once you calculate your time, you can focus on reducing cycle times to meet (or beat) it.
It also fits in perfectly with other lean principles. It’s compatible with pull systems, standardized work, and visual management to form a great framework for continuous improvement.
process improvement examples from different industries:
- An automotive parts manufacturer decreased lead times by 40% after aligning the process to takt time.
- A food processing plant increased throughput by 25% without adding another staff member after optimizing.
- An electronics assembly line reduced defects by 30% after using takt time to create a defect check station.
- These examples illustrate the power, if used correctly. You should expect similar results in your operation.
If you want to learn more about maximizing your impact using as few resources as possible, read our article on Lean Innovation. It’s a great companion piece as the same principles apply to takt time.
Optimizing Takt Time
Optimizing is a continuous process. It requires identifying waste and making constant improvements. I’ve walked many companies through this process, and the change in results can be dramatic.
To decrease time, the solution is almost always to remove waste. Determine any non-value-added activities you can eliminate or make more efficient. You might need to rearrange workstations, optimize material flow, or automate tasks.
Ensure TT is balanced with what your workers are capable of producing. If it’s too fast, the quality will be poor. If it’s too slow, you’re wasting resources. The goal is to find the perfect balance where output and quality are both maximized.
Technology can be extremely helpful to optimize takt time. Real-time monitoring, automated material replenishment, and predictive maintenance have all produced great results. These solutions help you maintain a consistent time and respond quickly if it’s not met.
When optimizing , don’t make these mistakes:
- Discarding worker ideas
- Only optimizing for speed, not quality
- Overlooking equipment maintenance
- Not adjusting as demand changes
Closing out
Always remember optimizing takt time is a process, not a destination. Continuously seek feedback and be open to making changes. If you’re persistent and pay attention to detail, you can make significant improvements to your production efficiency.
The journey to lean excellence is ongoing. Keep refining your processes and stay committed to continuous improvement. Your efforts will pay off in streamlined operations and a stronger bottom line.