Kaizen events are powerful tools for business improvement. I’ve led numerous events across various industries, consistently achieving remarkable results. These short, focused improvement sessions can transform your operations, boost efficiency, and engage your team. You’ll see rapid changes and long-lasting benefits. Let’s explore how Kaizen events can revolutionize your business.
Understanding Kaizen Events
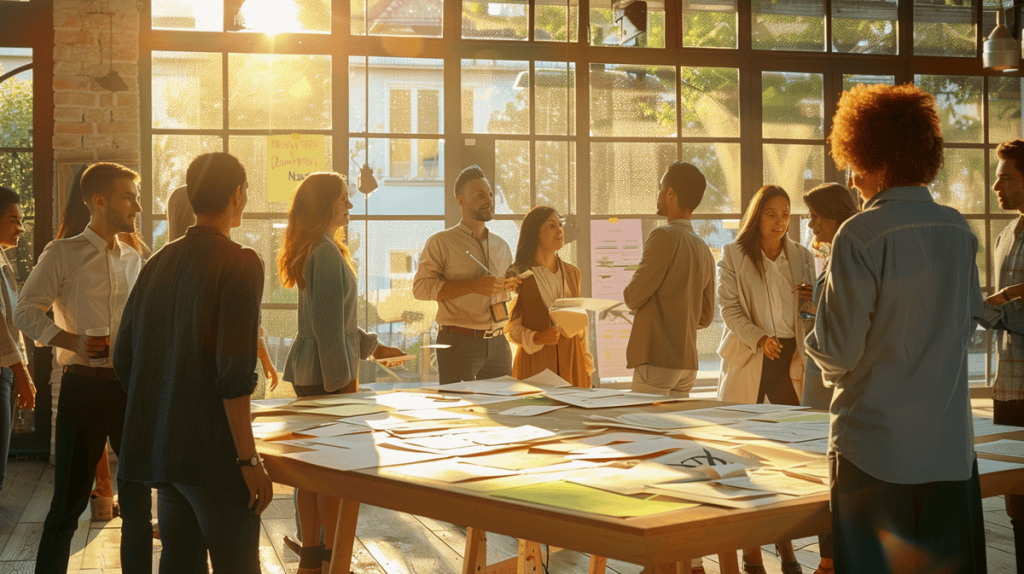
Kaizen events are structured improvement activities that aim to drive significant improvements in a short period of time within an organization. These projects utilize cross-functional teams working together to fix specific issues and/or improve processes. Kaizen events are designed to instill immediate progress and tangible results.
Kaizen is a concept that originated in Japan after World War II, and the word means “change” (kai) “good” (zen) in Japanese. It represents “change for the better,” and it’s based on the philosophy that continuous small improvements eventually lead to significant improvements over time.
Key attributes of a Kaizen event include:
- Short duration
- Limited scope
- Team activity
- Hands-on, data-driven structures
- Instant implementation of process changes
Kaizen events help to fix a variety of operational problems, such as eliminating waste, removing bottlenecks, improving quality, and increasing safety throughout the operation. They aren’t like other improvement methodologies because they are designed to deliver results quickly and empower frontline employees to drive change.
Benefits of Kaizen Events
As a lean management consultant, I’ve witnessed Kaizen events turn around struggling production lines. They are great for ongoing issues that never seem to go away, despite all of the problem-solving attempts an organization conducts.
Kaizen events are one of the best tools organizations have to make improvements. The primary benefit of Kaizen events is the speed at which you can make improvements. You can physically see, touch, and feel the changes you’ve made to a specific area immediately.
Employee engagement goes through the roof during Kaizen events because employees feel ownership and that they are making a difference in their work environment. As a result, they’ll typically be more productive and satisfied with their jobs.
Kaizen events force cross-functional collaboration, where employees from different departments come together and communicate in a way they likely never have before.
Nearly every Kaizen event results in some form of cost savings or process improvements. The impact to your bottom line can be significant.
You’ll build a culture of continuous improvement. Instead, employees will regularly identify problems and implement solutions to make small improvements to their respective tasks and areas.
While it’s not something as easy to measure, the long-term impact of cumulative small improvements from Kaizen events on organizational performance is significant. This has also been my experience in the field, as I’ve never seen a well-executed Kaizen event yield anything less than massive improvements to key performance indicators.
Planning a Kaizen Event
Selecting the right project and the right scope are essential to a successful Kaizen event. You need an area where improving the process will make a big impact, and the problem the process is facing can realistically be solved within the event’s timeframe.
Assembling the Kaizen team is a key step. The Kaizen team will generally be composed of 5-10 people from a mix of departments and levels within the company. The team will have various roles:
- Event facilitator
- Team leader
- Process owner
- Team members who work in and around the process
- Support staff (IT people, HR)
Setting specific, measurable, and aligned objectives and goals will give the team focus.
Ensure you have all of the data and resources ready before you begin the event to avoid wasted time. This includes historical data on process performance, process maps, and any other relevant information or documentation.
Developing a detailed event schedule will keep the team on track. A typical 5-day event might have a schedule like this:
Day 1: Orientation and current state analysis
Day 2: Idea generation and prioritization
Days 3-4: Implementation of quick wins and validation of solutions
Day 5: Standardization and presenting results
Prepare the event area and the materials you will need in advance to avoid wasting time. This includes setting up a dedicated room or area, ensuring you have all the necessary materials and supplies, and ensuring everyone has access to the systems or equipment they need.
How to Conduct a Kaizen Event
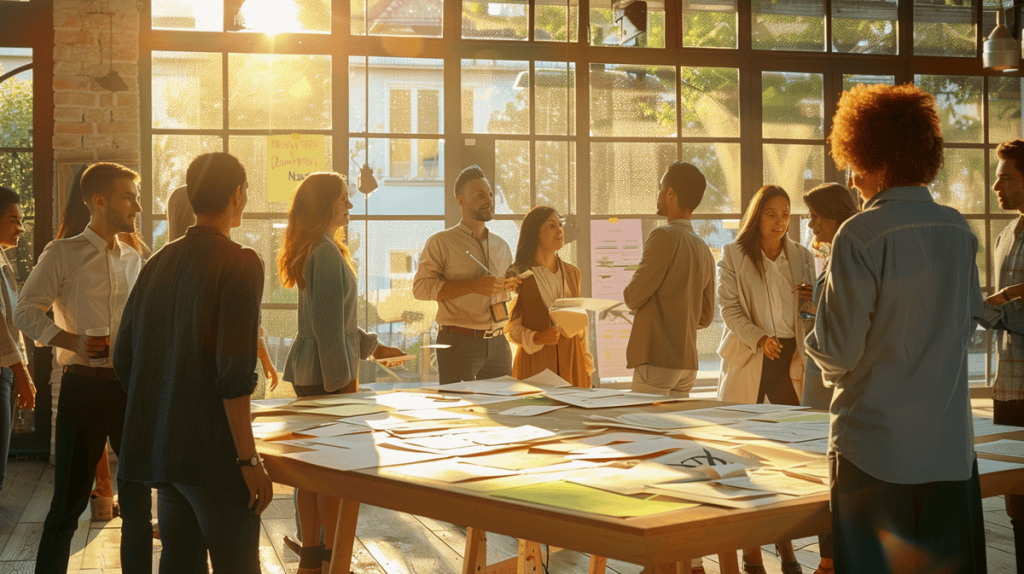
The kickoff meeting is critical, as it sets the tone for the event. During the kickoff meeting, you’ll outline objectives, set ground rules, and ensure participants are energized and feel a sense of urgency.
During current state analysis, you’ll map out the process and identify waste. The 8 Wastes of Lean are the most common type of waste to address in a Kaizen Event: Defects Overproduction Waiting Non-utilized talent Transportation Inventory Motion Over processing. I’ve found that visualizing the 8 Wastes makes it easier for teams to understand the scale of the opportunity.
The brainstorming and idea generation step is the most fun, as this is where the team gets to be creative. Brainwriting, reverse thinking, the SCAMPER method, and affinity diagram are all effective techniques.
Implementing quick wins and small improvements is important to keep momentum high. Focus on changes you can implement immediately without using many resources.
Testing and refining solutions is essential. The benefit of rapid experimentation is you can iterate and improve in real-time.
Standardizing a new process is how you ensure the improvement is sustained. Be sure to document the new standard, train employees, and establish a metric / KPI to monitor moving forward.
The final step is presenting your results and recommendations to leadership. This should encompass what you’ve fixed, what’s left to fix, and any key takeaways from the process.
Post-Event Actions
Ensuring that implemented changes continue to provide value is an important part of sustaining improvements. You’ll need to set KPIs to monitor and manage any problems that arise in the weeks following the event.
Capturing lessons learned and best practices helps refine the Kaizen process, so share these with the broader organization to improve future events.
Reporting results to stakeholders is important for gaining buy-in for future continuous improvement initiatives. Outline both the hard and the soft benefits of the Kaizen event.
Sustaining results after the event requires continued effort. Schedule regular check-ins and training sessions to ensure the new standard operates as it should.
Planning future Kaizen events ensures you continue to make progress. There’s always more improvement to achieve, so identify where you can continue making improvements and schedule your next event. Remember that Kaizen events should be focused on projects that have a 90- to 120-day lifespan.
Making Kaizen a part of the daily routine is the long-term goal. Encourage employees to practice Kaizen in their day-to-day work, and you’ve truly built a culture of continuous improvement.
Challenges and Pitfalls of Kaizen Events
Common challenges with Kaizen events include resistance to change, lack of leadership support, and inadequate resources. Address these challenges before they derail your Kaizen event.
Resistance to change can be mitigated through effective communication, involving the people who will be impacted by the change, and showing quick wins.
Maintaining momentum after the event is difficult. Schedule regular check-ins, recognize participants, and ensure continued leadership support.
Balancing short-term wins with long-term strategy is critical. Quick wins are great, but make sure they ladder up to the broader strategy of the business.
Prevent scope creep and overcommitting to a project by staying true to the event’s defined objectives.
Ensuring the right resources are in the room often requires pre-planning and gaining support from leadership. Make sure you have the resources you need before kicking off the event.
It’s worth noting that Kaizen events are not a good fit for every problem. They key specifically to problems that aren’t solved through statistical analysis over time. In those cases, another methodology may be best.
Best Practices for Successful Kaizen Events
Leadership support and involvement – It’s essential for leadership to actively champion the event, be present for key actions, and eliminate roadblocks for the team.
Clear communication – Keeping everyone informed and engaged throughout the process. This requires regular updates and open communication.
Proper training – Ensure team members have the proper training to contribute effectively. This may include training on Kaizen as well as specific project tools or techniques.
Focus on data – Encouraging the team to justify ideas with data and measurements. This is linked to the data-driven concept we discussed earlier.
Celebrate success and recognize – Recognizing team members drives motivation and builds momentum for future projects. Recognition and appreciation can go a long way.
Continuous improvement of the process – Always be improving Kaizen, the event itself. Reflect on what you could do better post-project after each event.
Kaizen events are powerful tools for rapid improvement. I’ve seen many times how they transform organizations. Remember to plan carefully select the right team and focus on achievable goals. Follow up is crucial. Sustain improvements and build on your success. With practice you’ll master the art of Kaizen events. They’ll become a cornerstone of your continuous improvement efforts. Your journey to operational excellence starts now.