The sound of machinery fills the air as we move through a busy factory. This noise shows productivity but also risk. Every sound could mean a possible breakdown, causing chaos. A bit poetic but we’ve all felt the dread of equipment failing at the worst time. Predictive maintenance to the rescue.
Its changed how we handle our equipment. It uses data and advanced analytics to predict problems before they start. This isn’t just about fixing things; it’s about making them run better and keeping our businesses safe from sudden downtime.
This article will show how predictive maintenance is changing industries. From factories to energy plants, companies are seeing its huge benefits. We’ll look at the technologies behind it and how to use it in your business.
Understanding the Basics of Predictive Maintenance
Predictive maintenance is key to keeping modern industries running smoothly. It uses data to predict when equipment might fail, so we can fix it before it breaks. By looking at patterns, we can stop problems before they start.
Condition monitoring is a big part of predictive maintenance. It checks the health of machines by looking at things like vibration, temperature, and oil levels. This helps us spot early signs of wear and tear.
Predictive maintenance is different from reactive maintenance that wait for things to break. It uses real-time data to know when maintenance is needed. This means less downtime and longer-lasting equipment.
Maintenance Type | Approach | Cost Efficiency | Downtime |
---|---|---|---|
Reactive | Fix after failure | Low | High |
Preventive | Fixed schedules | Moderate | Moderate |
Predictive | Data-driven | High | Low |
Key Benefits
One big plus is less downtime. By keeping an eye on things and analyzing data, we can spot problems early. This means repairs can be planned, not rushed, keeping production smooth and boosting output.
Another big win is making equipment last longer. Fixing small problems early stops them from getting worse. This cuts down on the need for expensive replacements and makes the most of costly equipment.
Being able to predict failures also makes workplaces safer. We can catch hazards before they happen, protecting workers and preventing accidents. This keeps employees safe and helps companies meet safety laws.
Benefit | Impact |
---|---|
Reduced Downtime | Decrease in unplanned outages |
Extended Equipment Life | Increased in machinery lifespan |
Improved Safety | Reduction in workplace accidents |
Cost Savings | Decrease in maintenance costs |
Essential Technologies Driving Predictive Maintenance
Predictive maintenance technologies have changed how we manage equipment. We now see more tools that use sensor data to make operations better. Let’s look at the main technologies leading this change.
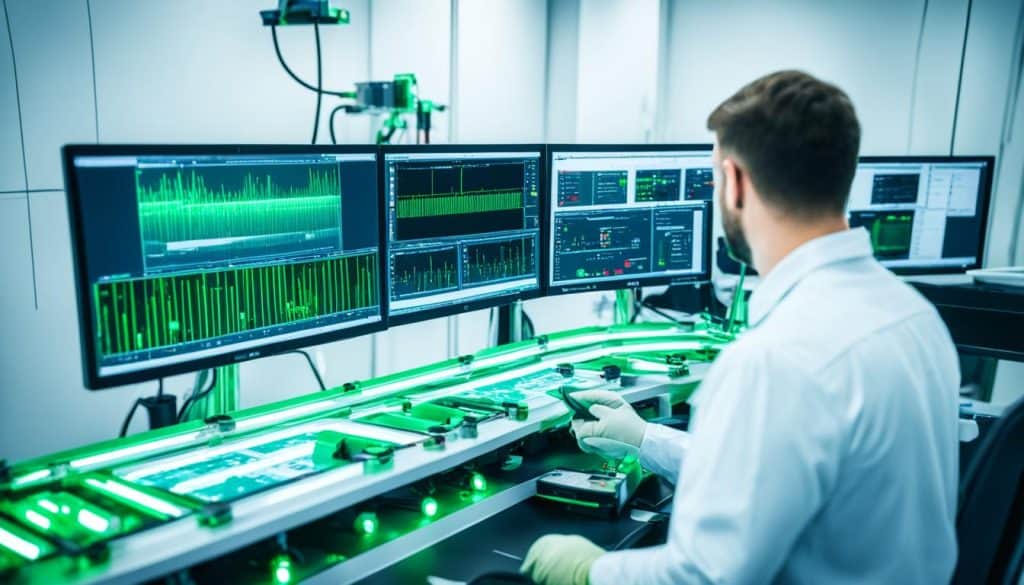
IoT sensors are key to today’s predictive maintenance. These small devices gather important data on how equipment works, its temperature, and vibrations. By always watching the machines, we can find problems before they get worse.
Big data analytics is vital for handling lots of sensor data. It uses smart algorithms to look for patterns and guess when maintenance is needed. This way, we can stop sudden breakdowns and make equipment last longer.
Cloud computing makes it easy to store and get to sensor data from anywhere. This lets maintenance teams check on equipment from afar and make fast decisions.
Technology | Function | Impact |
---|---|---|
IoT Sensors | Collect real-time data | Early detection of issues |
Big Data Analytics | Process and analyze data | Predict maintenance needs |
Cloud Computing | Store and access data remotely | Improve decision-making speed |
By using these predictive maintenance technologies together, we can make systems that make equipment work better and cut downtime.
The Role of Sensor Data in Equipment Monitoring
Sensor data analysis is key in today’s equipment monitoring. We use sensors to get real-time info on how machinery is doing. They track things like temperature, vibration, pressure, and noise levels. This info helps us understand how well our equipment is working.
Monitoring equipment with sensor data has a few steps. First, sensors are put on important parts of machines. They keep sending data, which goes to a main system. Then, advanced tools turn this data into useful info.
- Temperature sensors detect overheating issues
- Vibration sensors identify imbalances or misalignments
- Pressure sensors monitor fluid levels and system integrity
- Acoustic sensors detect unusual noises indicating potential problems
Systems that use sensor data for monitoring move us from reacting to predicting maintenance needs. This change saves money, makes things safer, and boosts productivity in many fields.
Condition Monitoring: A Cornerstone of Predictive Maintenance
Condition monitoring is key to good predictive maintenance. It helps us watch over equipment health closely. This way, we avoid sudden breakdowns and keep things running smoothly.
Vibration analysis is a big part of this. By looking at equipment vibrations, we can catch problems early. Issues like misalignment or wear on bearings can be spotted before they cause big trouble.
Oil analysis is also vital. We check oil samples for things like dirt, wear particles, and changes in viscosity. This tells us how well machines are doing and when it’s time for an oil change.
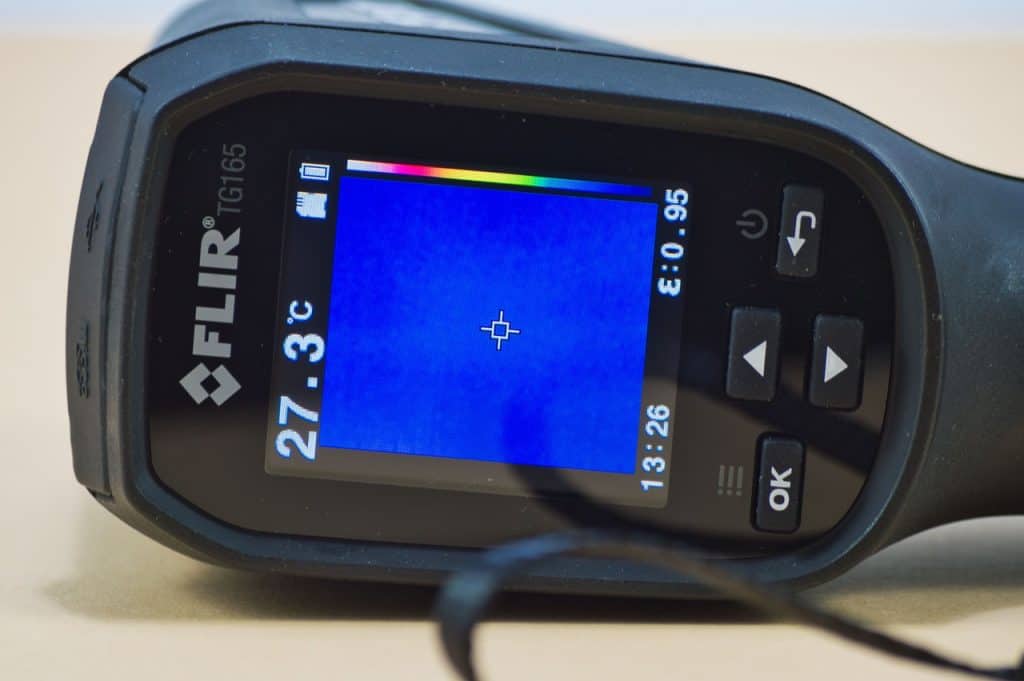
Thermography, or infrared imaging, lets us see overheating parts or electrical problems that are hard to spot by eye. It’s a great way to check electrical and mechanical parts without opening them up.
Real-time monitoring takes condition monitoring further. With sensors sending data non-stop, we can watch equipment performance all the time. This means we can spot problems right away and act fast.
Monitoring Technique | Application | Benefits |
---|---|---|
Vibration Analysis | Rotating equipment | Early detection of mechanical faults |
Oil Analysis | Engines, gearboxes | Improved lubrication management |
Thermography | Electrical systems | Identification of hotspots and insulation issues |
Real-time Monitoring | All equipment types | Continuous data collection and instant alerts |
Prognostics and Health Management (PHM) in Industry
Prognostics and health management (PHM) is changing how we maintain industrial equipment. It uses advanced tech to predict and stop equipment failures before they happen. PHM systems gather data from sensors, past records, and environmental factors.
PHM has shown great results in many industries. Here are some key benefits:
- Reduced unplanned downtime
- Improved safety and reliability
- Optimized maintenance schedules
- Lower operational costs
- Extended equipment lifespan
Industry | PHM Application | Key Benefits |
---|---|---|
Aerospace | Engine health monitoring | Enhanced safety, reduced maintenance costs |
Manufacturing | Production line optimization | Increased efficiency, minimized downtime |
Energy | Wind turbine performance tracking | Improved energy output, extended asset life |
As PHM grows, we’ll see more advanced uses in different areas. The mix of artificial intelligence and machine learning will make PHM systems more precise and effective. This will shape the future of keeping industrial equipment running smoothly.
Implementing a Successful Predictive Maintenance Program
Starting a predictive maintenance program needs careful planning and action. We first look at our current maintenance ways to see where we can get better. This means checking how equipment works, looking at maintenance records, and figuring out repair costs.
Then, we pick the right technologies for our maintenance plan. This could be sensors, data analytics software, and algorithms that learn from machines. The choice depends on what equipment we have and how much we can spend.
To make sure it works well, we follow these best practices:
- Start with a pilot project on critical equipment
- Set clear goals and metrics for success
- Regularly review and adjust the program
- Foster a culture of continuous improvement
- Integrate predictive maintenance with existing systems
Remember, making it work takes time and effort, but the benefits are huge in the long run.
Overcoming Challenges in Predictive Maintenance Adoption
Starting with predictive maintenance has its hurdles. Companies often face issues with data quality. If the data is not complete or wrong, it can mess up the predictions. This makes the whole process less reliable.
Another big challenge is combining new systems with old ones. Many companies struggle to link advanced predictive tools with their current systems.
People within the organization might resist changing to new tech. They might worry about losing their jobs or finding it hard to learn new things. To beat these challenges, we suggest starting small. Begin with a pilot project to show the benefits and gain trust. Then, offer training to help your team learn and feel secure.
To make data better, focus on collecting and cleaning it well. When integrating new tech, pick vendors who offer flexible solutions that fit your current setup. By focusing on these areas, we can make predictive maintenance work well and bring out its benefits.
- Conduct regular data audits to ensure accuracy
- Choose scalable predictive maintenance solutions
- Develop a change management strategy to address resistance
- Establish clear metrics to measure success and ROI
Getting Started: Next Steps
Are you ready to start with predictive maintenance? We’ve made a guide to help you begin this important strategy. Our guide offers a step-by-step plan for a smooth start in your company.
First, check how ready you are. Look at your current maintenance methods, the health of your equipment, and how you collect data. This step is key to finding what needs to get better and planning for success.
Then, set clear goals for your predictive maintenance. Decide on important performance indicators (KPIs) that match your business goals. These could be things like less downtime, longer equipment life, or better safety.
Step | Action | Expected Outcome |
---|---|---|
1 | Conduct readiness assessment | Identify areas for improvement |
2 | Set clear goals and KPIs | Align program with business objectives |
3 | Select appropriate technologies | Ensure effective data collection and analysis |
4 | Train staff and implement program | Successful adoption and execution |
Remember, making predictive maintenance work takes commitment and ongoing improvement. Start small, learn from early wins, and grow your program in your company.
Conclusion: Embracing the Predictive Maintenance Revolution
Predictive maintenance is changing the game for industries all over the world. It’s not just a new tech trend. It’s a smart way to keep machines running well and save money. The benefits are clear: less downtime, lower costs, and happier customers.
In today’s world of Industrial Revolution 4.0, staying ahead means embracing new tech. Predictive maintenance fits right in with this mindset. It uses data and smart algorithms to spot problems before they become big headaches. This approach helps companies stay ahead and avoid costly surprises.
We’re at a turning point in how we take care of machines. Predictive maintenance isn’t just nice to have – it’s becoming a must-have. Companies that jump on board now will be ready for whatever comes next.