Hi everyone, What I want to cover in this article is examine Failure Mode and Effects Analysis(FMEA). It may sound complicated if its your first time encountering the term but by the end you should have a good understanding.
What Exactly Is FMEA?
Essentially FMEA allows you to spot problems before they happen or that’s the key idea at least. The idea being to achieve a more preventative approach. The process originates from the space industry in the 1960s . A key driver was Engineers working on rockets needed a way to find problems on the ground before potential disastrous consequences.
It’s not limited to rocket science anymore and is widely used in many industries. At its core, FMEA involves breaking down a process, product, or system into its smallest parts. Then at it most basic level you ask “What could go wrong here?”
You approach it by examine what could be potential failures. From this determine their severity, likelihood, and how you might detect them. By doing this systematically, you create a map of potential pitfalls – and more importantly, a plan to avoid them. It’s proactive problem-solving at its finest.
Why use FMEA?
- Improving reliability
- Enhancing safety
- Reducing risks
These goals are central to FMEA’s value. When we discuss improving reliability, They key thing were looking at is to reduce failures or breakdowns. This ranges from car part lasting longer to a manufacturing process running smoother.
Safety is important in any industry. FMEA helps identify potential hazards. These hazards might harm people. They could also damage equipment or the environment. By spotting these risks early, we can implement safeguards to prevent accidents.
Risk reduction is crucial. It minimizes the chances of errors and mitigates their impact. FMEA offers a structured approach to this process. Through FMEA, we can systematically assess and prioritize risks—allowing us to concentrate our efforts where they’ll be most effective. This method ensures we address the most significant potential issues first.
FMEA is a predictive tool for quality and safety. It goes beyond mere reaction to problems; instead, it empowers you to prevent issues entirely. This proactive approach makes FMEA invaluable for process improvement.
its not a one-size-fits-all. There are several types, each with its own focus:
Design FMEA: This focuses on catching flaws in product design. It’s like having a meticulous critic reviewing your plans.
Process FMEA: Here, we’re focusing on risks in manufacturing or assembly. Think of it as a protective measure for your production line.
System FMEA: This takes a comprehensive view, examining how all the pieces fit together. It’s like being an investigator for system-level failures.
Service FMEA: Not just for manufacturing! This type helps service industries avoid customer disappointment.
Key Components of FMEA
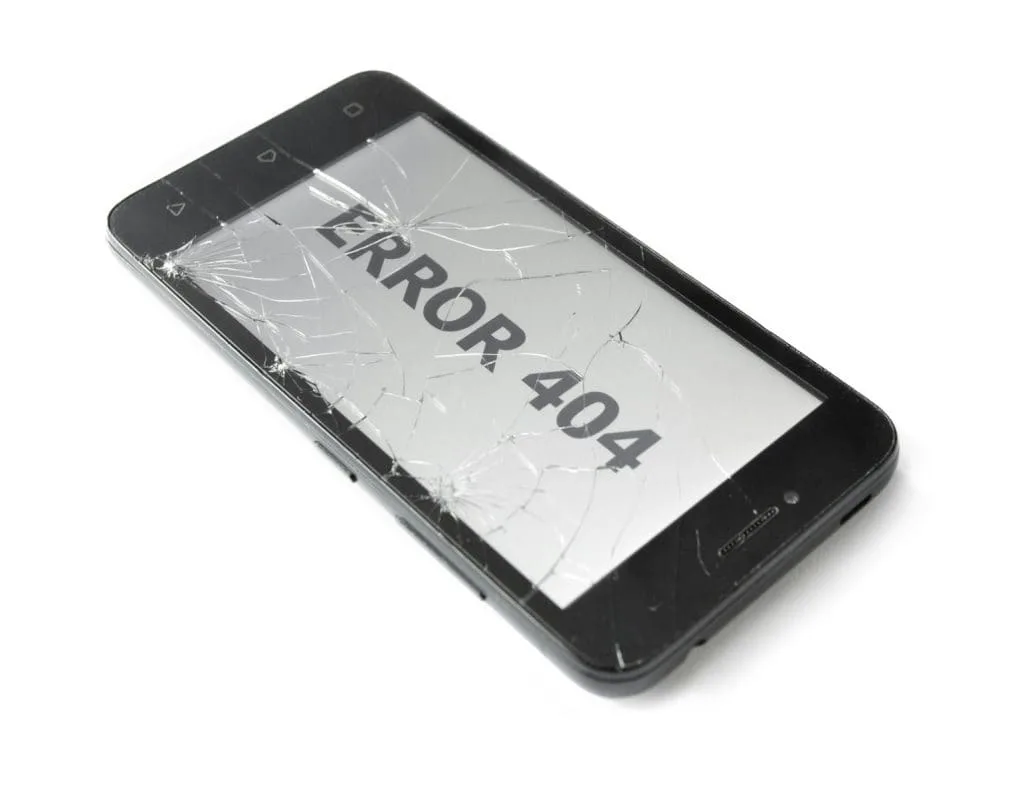
There are five main elements that make it effective:
Failure Modes: These are the ways things could go wrong. Think of them as the “what ifs” of your process or product.
Effects: The consequences of each failure. It’s the “so what” part of the equation.
Causes: The reasons behind the failure. This is where you investigate thoroughly.
Detection Methods: How you’ll catch these failures. It’s like setting up early warning systems for problems.
Risk Priority Number (RPN): This is the key figure that helps you prioritize. More on this later!
These components work together to give you a comprehensive picture of your risks.
Step-by-Step: The FMEA Process
Let’s break down how to actually perform an FMEA. It’s not overly complex, but it does require effort:
- Assemble your team and define what you’re examining.
- Break down your process, product, or system into manageable parts.
- Think critically and consider all the ways things could go wrong.
- Determine what would happen if each of those failures occurred.
- Identify what might cause each failure.
- Assess what controls you already have in place.
- Calculate numbers to prioritize your risks (that’s where the RPN comes in).
- Generate ideas to address the significant risks.
- Implement those fixes.
- Review and evaluate how well your changes worked.
Calculating Risk: Assessment Criteria
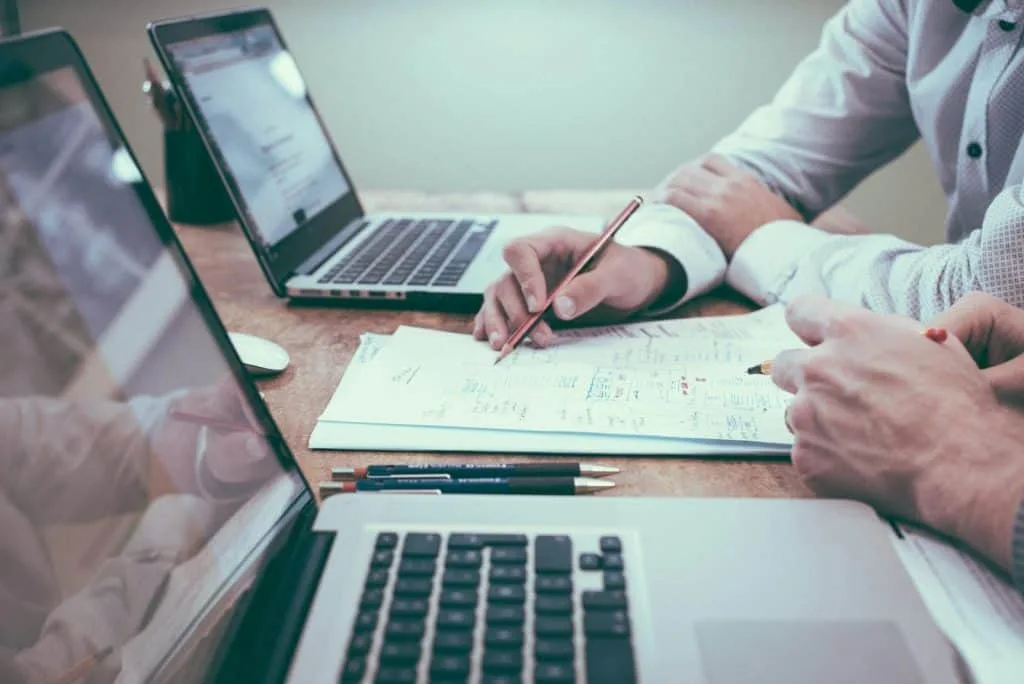
Now, let’s discuss that Risk Priority Number (RPN) mentioned earlier. It’s based on three factors:
Severity: How bad would it be if this failure happened? (Scale of 1-10)
Occurrence: How likely is it to happen? (Also 1-10)
Detection: How easy is it to spot before it causes problems? (Again, 1-10)
Multiply these three numbers together, and you’ve got your RPN. The higher the number, the more attention that risk needs.
Let’s examine these factors more closely:
Severity is about impact. A score of 1 might be a minor inconvenience, while a 10 could be catastrophic – think safety hazards or major financial losses. When assigning severity scores, envision the worst-case scenario. What’s the extended effect of this failure?
Occurrence is about frequency. How often might this failure appear? A 1 could be something that happens very rarely, while a 10 is an issue you’re dealing with constantly. Historical data can be very helpful here if you have it.
Detection is more nuanced. It’s not about how easy it is to fix the problem, but how likely you are to catch it before it causes trouble. A 1 means you’ve got highly effective detection methods in place, while a 10 suggests you might not know about the failure until it’s too late.
When you multiply these together, you can end up with RPNs ranging from 1 to 1000. But don’t focus too much on the exact number. The real value is in how it helps you prioritize.
For example, consider two potential failures:
Severity: 9, Occurrence: 2, Detection: 4. RPN = 72
Severity: 5, Occurrence: 8, Detection: 7. RPN = 280
The second one has a much higher RPN, so it might seem like the bigger priority. But pause for a moment – the first one has a severity of 9! Even though it’s less likely to happen, the consequences could be severe.
This is why it’s important to: use the RPN as a guide, but don’t let it be your only decision-making tool. It’s a great starting point for discussions and helps ensure you’re not overlooking any critical risks.
Remember, the goal isn’t to eliminate all risk – that’s impossible. It’s about managing risk effectively. Use these criteria to focus your efforts where they’ll have the biggest impact. And always be ready to reassess as conditions change. After all, continuous improvement requires ongoing vigilance and adaptation!
The FMEA Worksheet: An Essential Tool
The FMEA worksheet is where all this analysis happens. It’s like a detailed spreadsheet. Here’s what you’ll typically find:
- Columns for each step of the process
- Spaces to record potential failures, effects, and causes
- Spots to rate severity, occurrence, and detection
- A place to calculate that important RPN
Advice: Keep your language clear and specific. “Thing might break” isn’t nearly as helpful as “Gear tooth could shear off due to metal fatigue.”
Advantages and Limitations of FMEA
Like any tool, FMEA has its strengths and weaknesses. Let’s examine them:
Advantages:
- Identifies problems before they happen (saving money and resources)
- Improves product and process safety
- Reduces costs in the long run
- Helps focus resources where they matter most
Limitations:
- Can be time-consuming if not managed well
- Effectiveness depends on the team’s expertise
- People can sometimes be biased in their ratings
- It can be challenging to apply to complex, interconnected failures
Best Practices: Maximizing FMEA’s Effectiveness
From extensive experience, here are some key strategies:
- Include a diverse team. Someone from accounting might notice something an engineer missed.
- Prioritize your high-risk areas. Don’t waste time on minor issues.
- Use clear, specific language. It’ll prevent confusion later.
- Keep your FMEA current. It’s an ongoing document, not a one-time effort.
- Don’t fixate on the RPN. Use your judgment too.
- Create an environment where people feel comfortable speaking up. You want to encourage creative thinking!
These practices aren’t just theoretical – they’re proven strategies that can significantly impact your FMEA efforts. Teams often struggle when they treat FMEA as a box-ticking exercise, rushing through it with a homogeneous group.
That approach often leads to missed opportunities and blind spots. Instead, approach FMEA as a collaborative, ongoing process. Encourage innovative thinking and be willing to challenge assumptions. Remember, the goal isn’t to create a perfect document –
it’s to improve your processes and products continuously.
By promoting open communication and continuous learning, you’ll get the most value out of your FMEA efforts. The payoff in terms of reliability, safety, and efficiency is well worth the investment in doing FMEA properly.
FMEA Software options
There’s plenty of software available for FMEA. Here’s what to look for:
- User-friendly interface (because complicated software isn’t helpful)
- Collaboration features (team effort is crucial)
- Customizable templates (flexibility is important)
- Integration with other quality systems (compatibility matters)
Choosing FMEA software requires careful consideration of your industry and organizational needs. Highly regulated sectors like aerospace or medical devices may benefit from ReliaSoft XFMEA. It offers comprehensive risk analysis tools and supports various FMEA types.
For organizations with distributed teams, Intelex FMEA or QT9 QMS FMEA might be more appropriate. These options boast robust collaboration features and mobile accessibility.
Scalability and integration capabilities are crucial factors. SoftExpert FMEA, part of a broader quality management platform, could be ideal for small to medium-sized businesses seeking an integrated solution.
Real-World FMEA: Success Stories
FMEA successes aren’t just theoretical—they’re practical solutions with real impact. Throughout my career, I’ve witnessed firsthand how this approach saves companies time and money while preventing issues.
Let me share some cases with you. They illustrate FMEA’s power when applied thoughtfully.
These examples demonstrate significant improvements in reliability, safety, and overall quality. You’ll see how proactive problem-solving can truly transform operations.
Case Study 1: The Leaky Valve Issue
A chemical plant was experiencing valve failures leading to small leaks. We conducted a Process FMEA and found that the current maintenance schedule wasn’t detecting wear and tear quickly enough. By adjusting the inspection frequency and criteria, we reduced valve-related incidents by 75% in six months.
Case Study 2: Software Security Enhancement
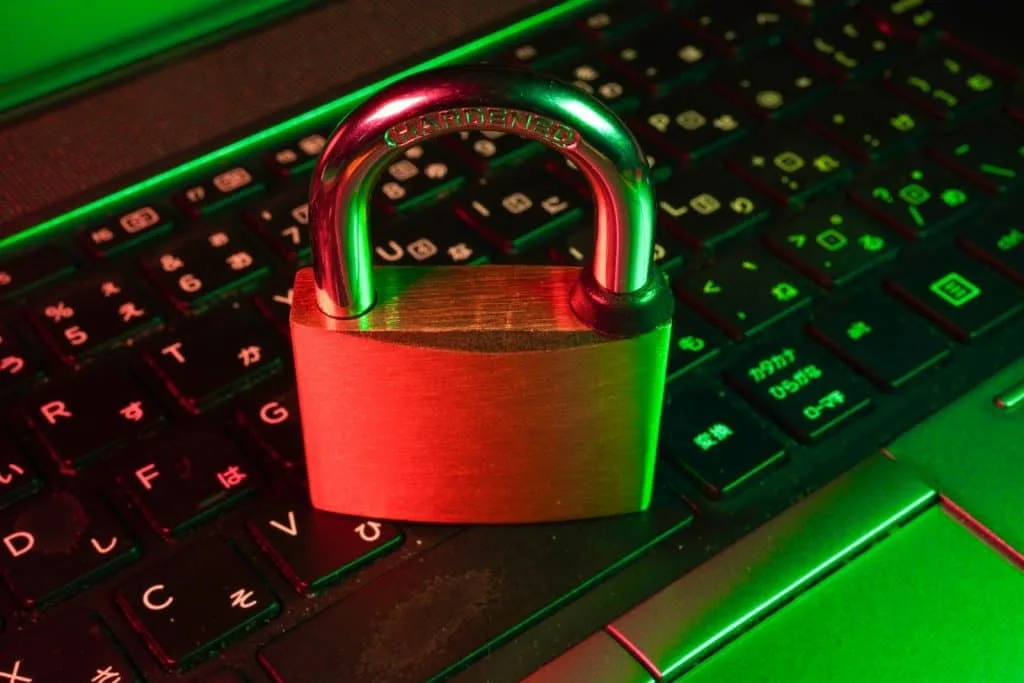
A tech startup was concerned about potential security vulnerabilities in their new app. We used a Software FMEA to identify high-risk areas in the code. This led to a redesign of the authentication process, preventing a potential data breach before the app even launched.
The takeaway? FMEA isn’t just paperwork. When done effectively, it delivers tangible results.
Conclusion
While FMEA requires significant initial effort, the results justify the investment. Consider it a protective measure for your processes and products, similar to how insurance protects your assets. Finding and fixing problems early helps save time and money. It also prevents larger issues from developing later. Remember, FMEA is most effective when everyone in your company participates. Involve people from different departments. Consider all ideas and be open to new perspectives.
The more you use FMEA, the better you’ll become at identifying potential problems in your work. This skill is valuable for continuous improvement.
Are you prepared to implement FMEA in your company? It’s a method to address risks before they become actual problems. If you use FMEA, your company will likely see significant benefits over time.