Introduction to Poka Yoke
Poka Yoke, a Japanese term meaning “mistake-proofing,” is an important concept in lean manufacturing. It originated in Toyota’s production system. It focuses on prevention rather than detection of errors.
The concept is simple: design processes to make errors impossible. We can by eliminating the possibility of mistakes create safer and more efficient workplaces.
The Psychology of Human Error
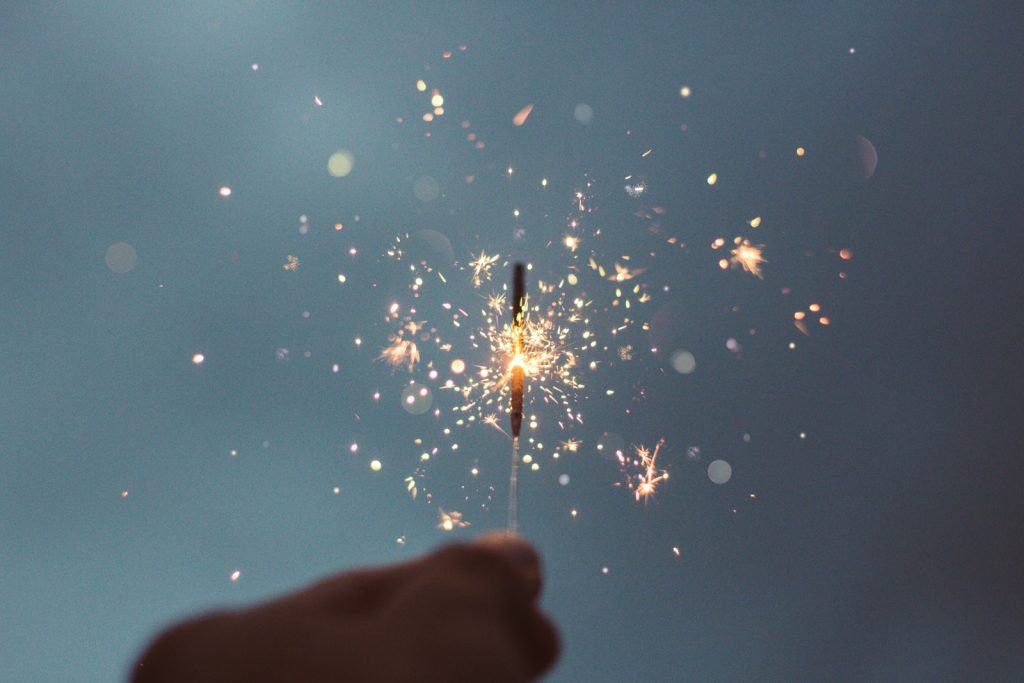
Its no surprise that we all make mistakes . Fatigue, distraction, and complacency are workplace constants. These factors contribute to a staggering number of accidents and near-misses daily.
Poka Yoke acknowledges this reality. Instead of relying on constant vigilance, it builds safeguards into processes. This approach ensures the human error effect on accidents is greatly reduced.
For instance, cognitive load theory tells us that our mental resources are limited. When we’re overwhelmed it can lead to mistakes happening. Poka Yoke reduces this cognitive burden, allowing workers to focus on value-adding tasks but also working safety.
Key Poka Yoke Techniques
Over the years, I’ve seen Poka Yoke implemented in countless ways. These methods generally fall into three categories:
- Physical Poka Yoke: This involves designing parts or tools that can only be used correctly. Think of a USB port that can only be inserted one way.
- Procedural Poka Yoke: These are step-by-step processes that guide workers through tasks. Checklists in aviation are a classic example.
- Visual Poka Yoke: Using color coding, symbols, or shapes to prevent errors. Traffic lights are a ubiquitous form of visual Poka Yoke.
Each technique has its place. The key is choosing the right method for the task at hand.
Implementing Poka Yoke in Safety Protocols
Implementing Poka Yoke isn’t rocket science, but it does require careful planning. Here’s a simplified roadmap:
- Identify error-prone processes
- Analyze the root causes of errors
- Brainstorm Poka Yoke solutions
- Test and refine your ideas
- Implement and monitor results
Remember, the goal is to make the right way the easy way. Your Poka Yoke solutions should seamlessly integrate into existing workflows.
Examples: Poka Yoke Improving Safety
Engineers at a manufacturing plant modified guarding to suit the size of manufactured parts being produced, thus stopping hand contact and preventing finger injuries. The existing machine guards were not fully effective for smaller parts, leaving gaps where operators’ fingers could potentially reach moving components. The engineers modified the guarding to improve safety.
A laboratory introduced color-coded lab coats – blue for general use and red for handling mild irritants, which reduced the risk of accidental exposure to chemicals. The lab implemented this system after noticing that researchers sometimes forgot which coat they had worn while working with specific substances. This simple color-coding made it immediately obvious which coats were potentially contaminated with irritants, preventing mix-ups and reducing skin exposure incidents.
A construction company implemented a floor marking system for equipment placement when not in use, which reduced the risk of slips, trips, and falls. They used durable, high-visibility tape to create designated zones for various tools and machinery on job sites. The company trained workers to return equipment to these marked areas after use, keeping walkways and work areas clear. It also improved overall site efficiency as workers spent less time searching for misplaced equipment.
All of the above are fairly simple ideas but significantly reduced everyday safety risks and helped protect workers from accidents. These low-cost, high-impact solutions demonstrate that effective safety improvements don’t always require complex or expensive interventions. By focusing on practical, easily implemented changes, companies can create safer work environments and foster a culture of safety awareness among employees.
Benefits Beyond Safety
While safety is paramount, Poka Yoke offers additional benefits. Error-proofing naturally leads to improved quality. When mistakes are impossible then generally the added benefit is defects disappear.
Efficiency also gets a boost. Workers spend less time double-checking and correcting errors. This translates to increased productivity and reduced costs.
It can also enhance job satisfaction. Employees feel more confident and less stressed when they know mistakes are unlikely. This leads to better morale and lower turnover.
Overcoming Challenges in Poka Yoke Adoption
Despite its benefits, implementing Poka Yoke isn’t always smooth sailing. Resistance to change is common. Some workers may feel that error-proofing systems question their competence.
To overcome this its important to communicate changes. Thus its important to explain that Poka Yoke is about creating systems that support workers its not about replacing them. Involving employees in the early stages is critical yo getting buy-in.
Another challenge is the initial investment. While Poka Yoke often leads to long-term savings, upfront costs can be a barrier. To address this, start small. Implement low-cost solutions first to demonstrate ROI.
Lastly, avoid over-engineering. The best Poka Yoke solutions are often the simplest. Complexity can introduce new opportunities for error.
Future of Poka Yoke in Workplace Safety
As we look to the future, technology is set to revolutionize Poka Yoke. AI and machine learning offer exciting possibilities for predictive error-proofing.
Imagine systems that can anticipate mistakes before they happen. Or wearable tech that provides real-time guidance to workers. These aren’t science fiction they’re likely on the horizon in the future.
However, we must be cautious. Technology should enhance, not replace, human judgment. The future of Poka Yoke lies in finding the right balance between automation and human expertise.
Conclusion: Creating a Culture of Prevention
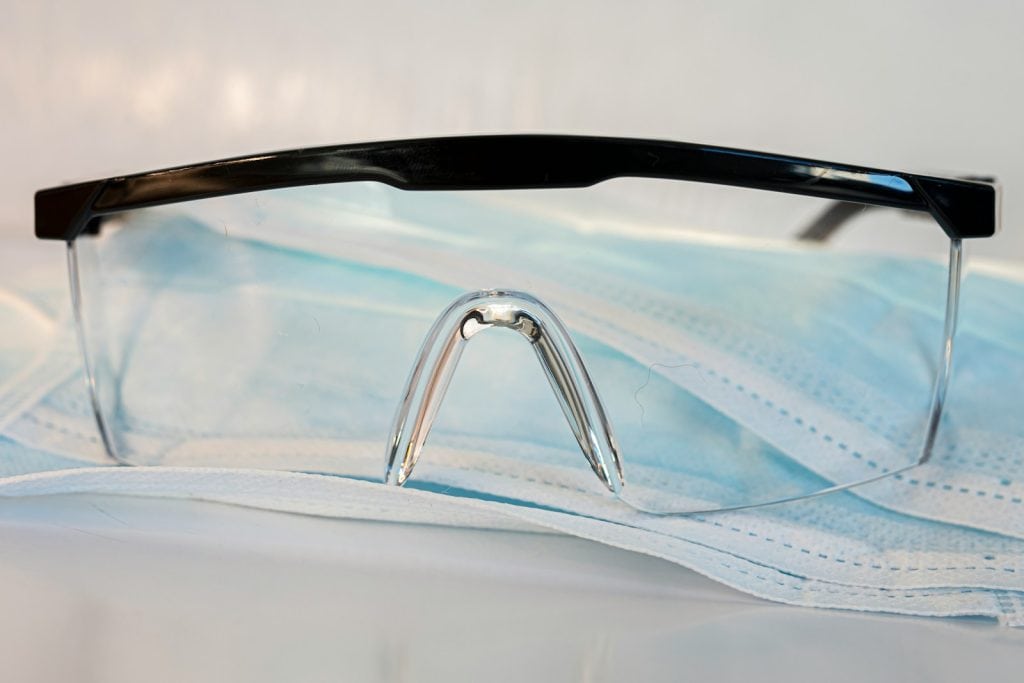
Poka Yoke is more than just a set of techniques. It’s a mindset. By embracing error-proofing, we create a culture of prevention.
This culture shift is crucial. In today’s fast-paced work environments, reactive safety measures aren’t enough. We need proactive strategies that anticipate and eliminate risks.
Its not always easy to implement Poka Yoke and It requires commitment, creativity, and sometimes, a willingness to challenge conventions. However the rewards related to terms safety, quality, and efficiency – are well worth the effort.
One key takeaway to remember that the safest workplace is one where accidents can’t happen in the first place. That’s the power of Poka Yoke. It’s not just about preventing errors; it’s about creating environments where excellence is the only option.
It doesn’t matter if your on the shop floor or in the boardroom. You should consider how Poka Yoke might transform your approach to safety. The life you save could be your own or that of someone who depends on you. In the world of workplace safety, an ounce of prevention truly is worth a pound of cure.