As a lean management consultant , I’ve seen my fair share of quality issues plaguing production lines. But every now and then, a solution comes along that reminds me why I fell in love with this field in the first place. Let me tell you about a recent project that perfectly illustrates the power of Poka-Yoke in action.
The Manufacturing Process
I got a call to consult for a mid-sized automotive parts manufacturer in the Midwest, not too far from where I first learned the ropes on the production line. They were wrestling with some serious consistency issues in their engine mount assembly process. Now, this is a critical component. Mess it up, and you’re looking at increased vibration, potential engine damage, and a massive warranty claim disaster waiting to happen.
Their process involved attaching the engine mount to the vehicle frame with four high-strength bolts. This sounds straightforward, But as any seasoned engineer will tell you, the devil’s in the details which in this case was the torque specifications.
The Quality Issue
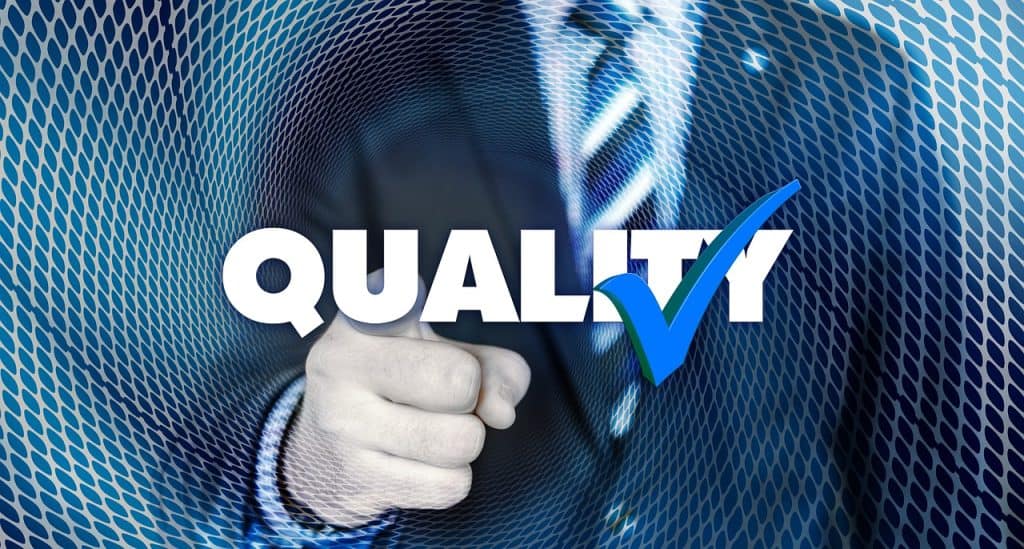
The problem was twofold. First, workers were occasionally missing a bolt entirely during the fast-paced assembly process. And secondly, and more importantly, even when all bolts were in place, they weren’t always tightened to the correct torque specifications. This led to a frustrating mix of obvious defects caught during quality checks and subtle issues that wouldn’t manifest until the product was with the customer.
The plant manager was tearing his hair out. They’d tried everything from additional training to increasing quality checks, but human error kept creeping in. That’s when I knew we needed a robust Poka-Yoke solution.
The Poka-Yoke Solution: Smart Torque Verification System
After a thorough analysis and brainstorming sessions with the line workers (always involve the folks on the ground, trust me), we developed what I like to call the Smart Torque Verification System (STVS).
Here’s how it works:
- Each engine mount station is equipped with a custom-designed fixture that holds the mount in place.
- The fixture has four precision sensors, one for each bolt location.
- We integrated a smart, variable-speed electric torque wrench with the system.
- A small display panel was installed at each workstation.
The magic happens when the assembly begins. The system won’t allow the next step in the process until all four bolts are detected in their proper locations. This immediately eliminates the “missing bolt” problem.
But here’s where it gets really clever. The smart torque wrench is programmed with the exact torque specification for each bolt. As the worker tightens each bolt, the system monitors the applied torque in real-time. The display provides visual feedback, shifting from red to yellow to green as the correct torque is approached and achieved.
If a bolt is under-torqued, the system won’t let the worker move to the next bolt. If it’s over-torqued, an alert is triggered instantly, summoning a supervisor to inspect the mount before it can proceed down the line.
The entire process is logged, providing a digital “torque signature” for every single engine mount that leaves the station. It’s quality assurance and traceability rolled into one slick package.
Impact on Quality and Productivity
The results were, frankly, stunning. Within the first month of implementation:
- Defects related to missing or improperly torqued bolts dropped by 98.7%.
- Overall first-time quality rate for the engine mount assembly improved from 94.2% to 99.9%.
- Surprisingly, productivity increased by 12%. Turns out, eliminating rework and providing clear visual guidance actually sped up the process.
The plant manager couldn’t stop grinning during our review meeting. “Alex,” he said, “I haven’t slept this well in years.”
implementation Challenges

Now, it wasn’t all smooth sailing. We hit a few snags during implementation:
- Initial resistance from some veteran workers who felt the system was “babysitting” them.
- A software glitch that caused false positives during the first week.
- Calibration issues with the torque sensors.
We tackled these head-on. For the worker resistance, we held open forums to discuss the system’s benefits and incorporated their feedback into the UI design. The software glitch was squashed with some late nights and plenty of coffee.
The key was maintaining open communication channels and demonstrating a willingness to adapt the system based on real-world feedback.
Cost Considerations and ROI
I won’t sugarcoat it – the initial investment was substantial. The total cost for developing and implementing the STVS across 10 assembly stations came to $275,000. That’s not chump change for a mid-sized operation.
However, the return on investment was rapid and significant:
- Reduction in warranty claims: $180,000 annually
- Decreased rework and scrap: $120,000 annually
- Productivity gains: Estimated at $250,000 annually
All told, the system paid for itself in just under 6 months. Beyond that, it’s pure profit – not to mention the incalculable benefit to the company’s reputation for quality.
Employee Feedback and Adoption
This is where things get interesting from a lean management perspective. Initially, as I mentioned, there was some pushback. But as workers began to use the system, something fascinating happened. They started to take pride in achieving “perfect torque” on every assembly.
We introduced a friendly competition, displaying weekly “torque scores” for each shift. Before long, workers were striving to maintain their 100% records. One line worker, Jim, told me, “It’s like a video game, but I’m building real engines. It’s actually pretty cool.”
The system also reduced stress. Workers no longer worried about making mistakes that could lead to major issues down the line. As Maria, a team lead, put it, “I used to lie awake wondering if I’d missed something. Now, I know every mount I touch is spot-on.”
Lessons Learned and Future Applications
This project reinforced several key principles of effective Poka-Yoke implementation:
- Involve front-line workers in the design process. They know the pain points better than anyone.
- Make the system intuitive and visually engaging. The “gamification” aspect was an unexpected bonus.
- You should be prepared to iterate. No solution is perfect out of the gate.
- Don’t underestimate the psychological benefits. Reducing worker stress can be as impactful as reducing defects.
Looking ahead, we’re exploring ways to expand the STVS concept to other critical assembly processes. There’s talk of integrating it with the plant’s MES (Manufacturing Execution System) for even greater traceability.
We’re also investigating the use of machine learning to predict potential torque issues based on subtle variations in the torque signatures. It’s an exciting fusion of traditional lean principles and cutting-edge AI – a direction I’m particularly passionate about.
In conclusion, this case study demonstrates the profound impact a well-designed Poka-Yoke system can have – not just on quality metrics, but on worker satisfaction and overall operational excellence. It’s a powerful reminder that in the world of lean manufacturing, creativity and technology can combine to solve even the most persistent challenges.
As I often tell my mentees, the best Poka-Yoke solutions don’t just prevent mistakes – they make it easier to do the job right than to do it wrong. The Smart Torque Verification System is a textbook example of this principle in action, and I couldn’t be prouder of the results.