Introduction to Poka-Yoke
Having spent years in manufacturing and process improvement, I’ve witnessed many quality control methods rise and fall. But one approach continues to transform our thinking on error prevention which is Poka-Yoke.
Poka-Yoke, which is Japanese for “mistake-proofing,” isn’t just another trendy term. It’s a robust approach that’s been quietly reshaping industries since the 1960s, when Shigeo Shingo introduced it at Toyota.
At its heart, its about designing processes and products to make errors nearly impossible. It’s simple yet powerful at the same time
The Psychology Behind Human Error
Let’s face it: we’re all human, and we all make mistakes. One key thing to consider most errors aren’t due to laziness or incompetence. They’re hardwired into our cognitive processes. From my time spent in continuous improvement, I’ve identified three main types of errors that Poka-Yoke addresses:
- Forgetfulness: Ever missed a key step because you were distracted? It’s common.
- Misunderstanding: Unclear instructions or assumptions can cause costly errors.
- Inadvertent errors: Sometimes we make mistakes, where all human.
Remember Its not about blame or fear. It’s about recognizing human limits and creating systems that work with our minds, not against them.
Key Elements of Poka-Yoke Implementation
Putting it into practice isn’t overly complex, but it does need a change in thinking. Here are the main parts:
- Process analysis: You can’t fix what you don’t understand. Dive deep into your workflows.
- Error identification: Pinpoint where mistakes are likely to occur.
- Solution design: Create mechanisms that prevent errors or make them immediately obvious.
- Testing and refinement: Poka-Yoke isn’t a “set it and forget it” solution. Continuous improvement is key.
- Training and buy-in: The best systems in the world are useless if your team doesn’t embrace them.
Techniques and Tools
In my years of consulting, I’ve seen Poka-Yoke implemented in countless creative ways. Here’s a quick rundown of some effective techniques:
Physical design: Think puzzle pieces that only fit one way or color-coded connectors.
Checklists and visual aids: Sometimes, the simplest solutions are the most effective.
Sensors and alarms: Technology can be a powerful ally in error detection.
Standardization: Reducing variability often reduces errors.
Fail–safes: Design systems that default to a safe state when something goes wrong.
Remember, the goal isn’t to create a one-size-fits-all solution, but to tailor these techniques to your specific processes and challenges.
Case Studies: Poka-Yoke Success Stories
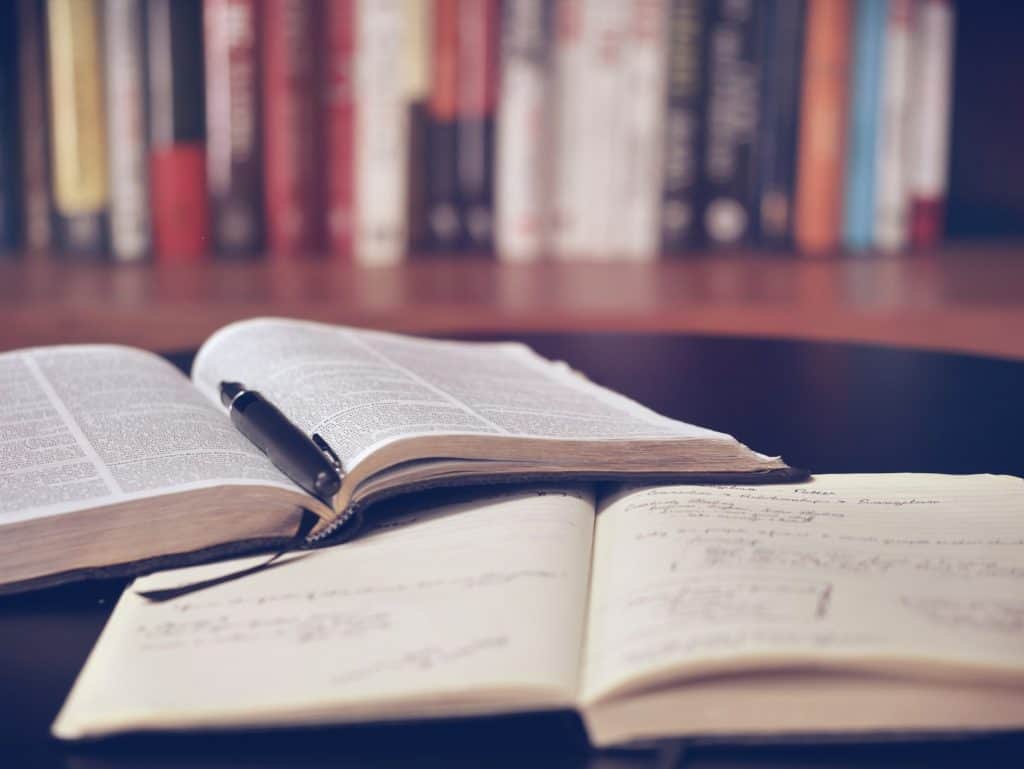
I’ve watched Poka-Yoke create impressive results in various industries. At one car factory, we used a basic color-coding system for assembly. The outcome? Errors dropped by 73% and productivity rose 15%.
In a drug company, using barcode scans and weight checks cut sorting mistakes by 9%. These aren’t just statistics – they show real gains in safety, quality, and efficiency.
Integrating with Lean Manufacturing
As someone who cut their teeth on lean principles, I can tell you that Poka-Yoke and lean manufacturing are a match made in efficiency heaven.
it supports lean goals by:
Reducing waste from defects and rework Improving flow by preventing bottlenecks caused by errors.
Enhancing standardization and stability in processes Supporting continuous improvement efforts
When integrated effectively, Poka-Yoke becomes not just a tool, but a fundamental aspect of your lean culture.
Overcoming Challenges in Adoption
Let’s not sugarcoat it when implementing Poka-Yoke its not always smooth sailing. I’ve encountered plenty of resistance in my career, often stemming from:
Cost concerns: “It’s too expensive to redesign our processes!”
Skepticism: “We’ve always done it this way, why change?”
Overcomplication: Sometimes, in our zeal to error-proof, we create overly complex systems.
The key to overcoming these challenges? Communication, education, and starting small. Show concrete results, and you’ll win over even the most stubborn skeptics.
Measuring Success
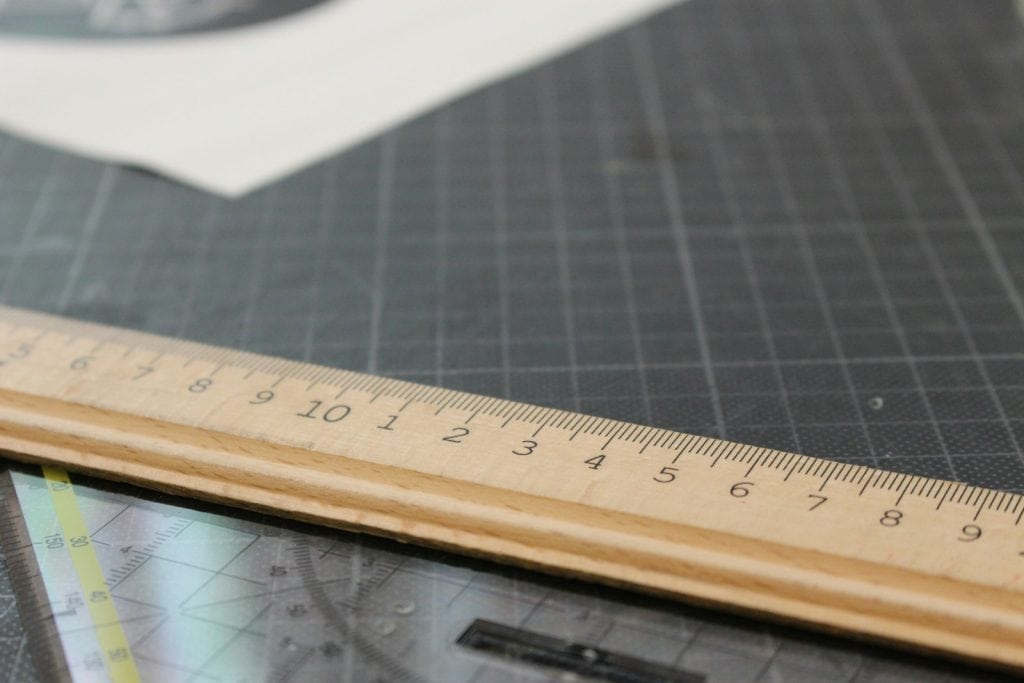
In our data-focused world, you need to show the worth of any new approach. Here’s how to measure impact:
- Compare defect rates before and after use
- Check the decrease in rework and its costs
- Look at improvements in production time and output
- See how it affects customer happiness and loyalty
From what I’ve seen, a good Poka-Yoke system can pay off in months, not years.
Future Trends: Poka-Yoke in the Digital Age
As we advance towards Industry 4.0, Poka-Yoke is evolving. I’m particularly keen on:
- AI and machine learning to foresee and prevent errors
- Augmented reality to guide complex tasks in real-time
- IoT sensors to spot errors more thoroughly
A key point is don’t get so focused on technology that you forget the basic ideas. Often, the most effective solutions are the simplest ones.
Conclusion: Building a Culture of Quality
After decades in this field, I can confidently say that Poka-Yoke is more than just a set of tools or techniques. It’s a mindset and a commitment to excellence that permeates every level of an organization. When implemented thoughtfully, Poka-Yoke doesn’t just prevent errors; it empowers workers, boosts morale, and drives continuous improvement.
As you start your Poka-Yoke journey to success, remember these key things:
Start small, but aim high. Begin with test projects, while envisioning company-wide adoption. Include your frontline staff. They often have the best ideas about error sources and prevention.
Celebrate wins, but don’t get complacent. There’s always room to improve. Stay inquisitive and keep learning. Poka-Yoke principles are timeless, but their applications keep evolving.
In today’s world, where quality can determine a business’s success, Poka-Yoke isn’t optional, it’s a must-have. So get started, examine your processes, and begin error-proofing. Your profits (and stress levels) will benefit.
Remember, in quality control, prevention beats cure. This might be the most impactful preventive measure you’ll ever use.