After decades in the trenches of lean management, I’ve seen countless workplace transformations. But nothing quite matches the elegant simplicity and profound impact of the 5S methodology. It can have a massive impact and I’m here to break it down for you.
Understanding the 5S Methodology
The 5S system is not just a trendy management term. its a tried and tested workplace organization strategy. Its been used within industries since the mid-20th century. The five S’s are highly effective for creating and maintaining an efficient, safe, and productive workplace.
From were I started on the factory floor to as my career progressed as a consultant. I’ve seen 5S work absolute wonders in manufacturing plants, healthcare facilities and even creative offices. It’s not about strict adherence to rules; Its about encouraging continuous improvement and a strong respect for the workspace.
Sort (Seiri): Decluttering for Clarity
The first step is often the most eye-opening. Sorting involves a brutal honesty about what’s necessary and what’s not. I’ve walked into workspaces that looked like glorified storage units – tools from the 1980s gathering dust next to cutting-edge equipment.
A good approach is to categorize everything:
- keep
- relocate
- toss.
Use red tags for items whose necessity is questionable. It’s amazing how much clearer thinking becomes when you’re not surrounded by clutter. I’ve seen productivity jump by 5-15% just from this step alone.
Set in Order (Seiton): Optimal Organization Strategies
After decluttering, it’s time to organize what’s left. It’s not about making things look nice but about maximizing efficiency. Ideally every tool and component should have a logical place where it belongs.
I’m a big fan of shadow boards for tools and color-coded zones for different work areas. Visual management is key – anyone should be able to walk into the space and immediately understand where things belong. Also, consider ergonomics: ensure frequently used items are easily accessible to minimize strain and unnecessary movement.
Shine (Seiso): Maintaining a Clean Workspace
Cleanliness isn’t just about looking good – it’s crucial for safety and making equipment last. At an automotive plant I worked at, daily cleaning routines cut machine breakdowns related to poor cleaning by 30%!
The key is to make cleaning a habit, not a hassle. Give team members specific areas, the right tools, and, time. Just five minutes at the end of each shift can save hours of downtime later.
Standardize (Seiketsu): Creating Consistent Processes
Standardization is where the real power of 5S starts to show. It’s about creating systems that make the first three S’s automatic. Standard Operating Procedures (SOPs) are your best friends here.
Visual aids are crucial – I’ve seen great success with color-coded charts, before-and-after photos, and even short video guides. Regular audits keep everyone accountable. Remember, the goal isn’t perfection, but consistent improvement.
Sustain (Shitsuke): Embedding 5S in Company Culture
Sustaining 5S is about transforming it from a program into a culture. It’s the hardest part, and I’ve seen many companies fail here.
The key is engagement at all levels. Leadership needs to walk the talk – I once saw a CEO personally participate in a sorting event, which sent a powerful message. Regular training, recognition programs, and open communication channels are essential. Make 5S part of performance reviews and onboarding processes.
Measuring 5S Success: KPIs and Metrics
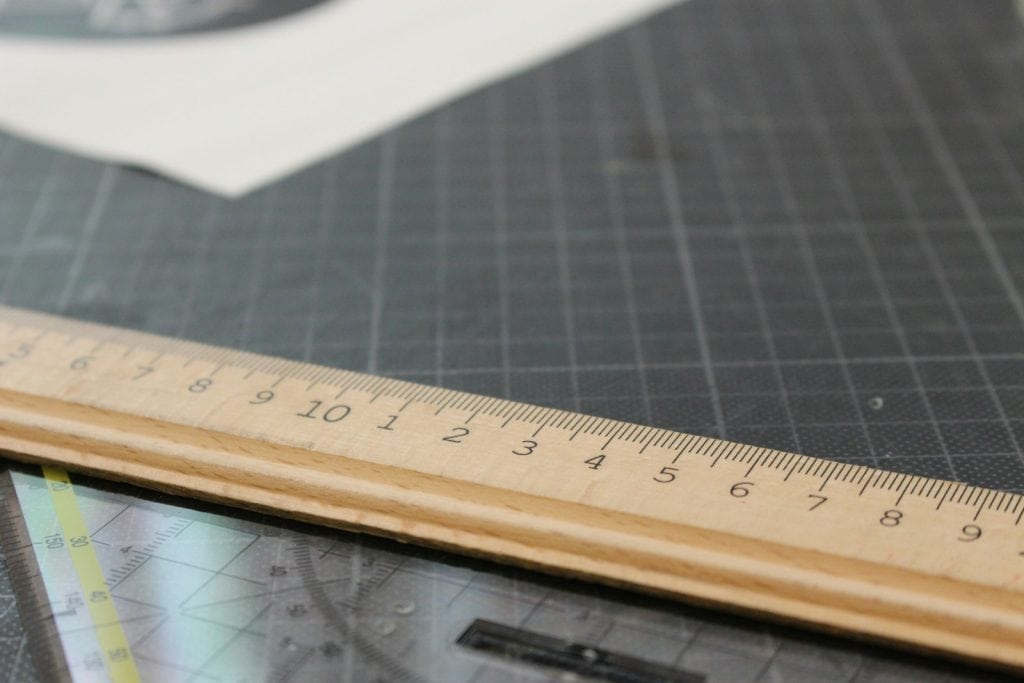
You can’t improve what you don’t measure. Tracking the right metrics is crucial for maintaining momentum and demonstrating ROI. Some key indicators I like to use include:
- Time saved in searching for tools/information
- Reduction in accidents and near-misses
- Improvement in on-time deliveries
- Decrease in defect rates
- Employee satisfaction scores
You shouldn’t just collect data make sure to use it. Regular review meetings to discuss these metrics can drive continuous improvement and keep everyone focused on the goals.
5S Beyond Manufacturing: Adapting to Different Industries
5S started in manufacturing, but it works everywhere! I’ve used 5S in call centers to cut response times and boost customer feedback. In software development, applying 5S to code repositories and environments has really sped up workflows.
The trick is to grasp the basics and tweak them for each industry. In a law firm, “Sort” might focus on digital files instead of physical stuff, but the idea stays the same.
Technology and 5S: Digital Tools for Modern Workplaces
In today’s digital age, 5S isn’t limited to physical spaces. There are numerous software tools that can support and enhance 5S efforts. Digital Kanban boards, cloud-based document management systems, and IoT sensors for equipment monitoring are just a few examples.
I’m particularly excited about augmented reality applications for visual management. Imagine being able to see optimal tool placements or cleanliness standards overlaid on your actual workspace through AR glasses. The potential is enormous.
Overcoming 5S Challenges: Addressing Common Pitfalls
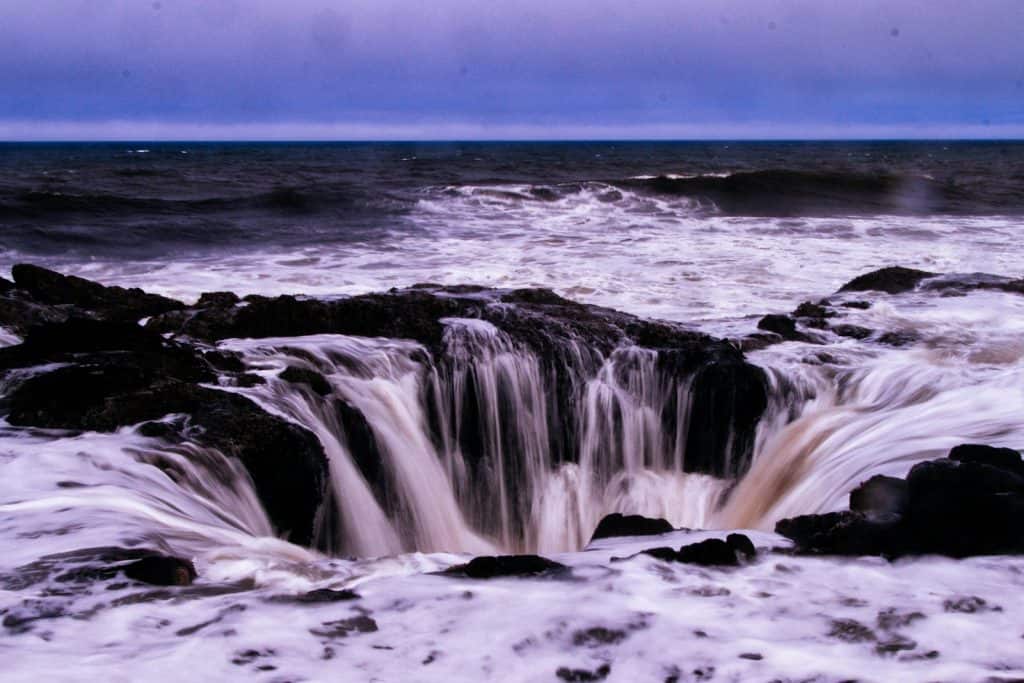
Anyone who has implementing 5S will know it isn’t always easy and people resist change. To tackle this, involve team members in planning and clearly explain the benefits.
If you have Limited resources them simply start small with a pilot area to show success before expanding. Creativity helps too. I’ve seen teams use colored tape and a label maker to create great visual management systems.
Keeping momentum is key. Host regular events, set up department competitions, and celebrate small wins to keep the energy high.
5S isn’t just a set of practices – it’s a philosophy of continuous improvement and respect for the workplace. When done right, it can transform not just your physical space but your whole organizational culture.
I’ve seen 5S turn struggling facilities into industry leaders and demoralized teams into engaged, proud workforces. It’s not always easy, but it’s worth it. So, roll up your sleeves, grab those red tags, and start your journey to a leaner, cleaner, and more productive workplace. Trust me, you won’t regret it.