As someone who’s spent decades in the area of lean management, I’ve seen my fair share of companies struggle with workplace organization and efficiency. One particular Engineering company I worked with which was a mid-size firm. Took the bull by the horns and revolutionized their operations with the 5S methodology. Their journey wasn’t just a tick-box exercise; it was a masterclass in Lean Transformation that would make even the most hardened skeptics sit up and take notice.
Company Background: The Chaotic Canvas
This company specializes in custom industrial automation solutions. It was the engineering environment that a lot of us have have dealt with best described as “organized chaos.” This ranged from workstations cluttered with components, tools scattered like breadcrumbs, and a stockroom that seemed to operate on its own mysterious logic. It was a powder keg of inefficiency just waiting to blow.
The company’s bread and butter was designing and fabricating automated systems for manufacturing plants. But ironically, their own manufacturing process was about as streamlined as a rush-hour traffic jam. Project delays common and not the exception. Often quality issues were creeping up like weeds in an untended garden.
Motivation: The Tipping Point
It wasn’t until a major client threatened to jump ship due to repeated delays that the company’s management realized they were sitting on a time bomb. They needed a radical change, and they needed it yesterday. That’s when they started using the 5S methodology in a attempt to bring order to their chaos.
Their goals were ambitious but necessary:
- Slash project completion times by 30%
- Reduce quality defects by 10%
- Boost employee productivity by 20%
- Transform their workspace into a model of efficiency
Lofty targets? Absolutely. But in my experience, if you’re not aiming high in lean management, you’re just rearranging deck chairs on the Titanic.
Implementation: The 5S Symphony
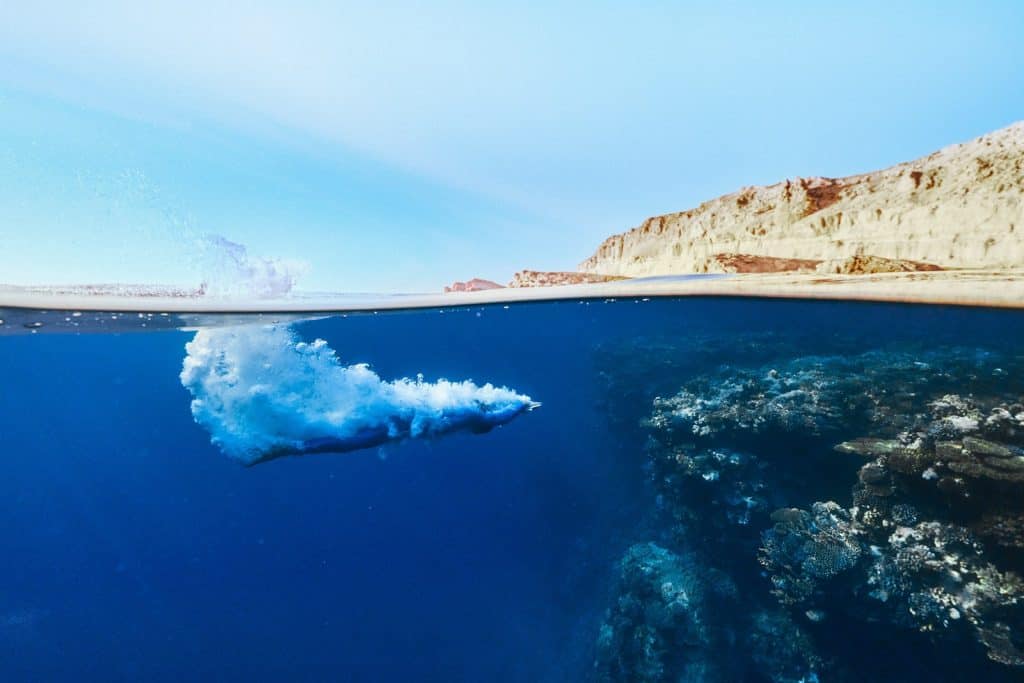
This company didn’t just dip their toes in the 5S waters; they dove in head first. They assembled a cross-functional 5S team which mixed seasoned engineers with fresh-faced technicians. This diversity was crucial as it brought together the wisdom of experience and the energy of innovation.
The team kicked off with a two-week intensive training program. I’ve seen too many companies skimp on training, but this company got it right. They brought in external lean experts (yours truly included) to drill the 5S principles into every employee’s DNA.
Then came the real work.
Let’s break it down:
a) Sort (Seiri): The Great Purge the company’s engineers were pack rats by nature, but we instituted a ruthless sorting process. Every item in the facility was evaluated. If it hadn’t been used in the past month, it was tagged for removal. The result was two dumpsters full of obsolete components and a collective sigh of relief from the cleaning staff.
b) Set in Order (Seiton): This is where the real magic happened. We redesigned workstations for optimal flow, created shadow boards for tools, and implemented a color-coded system for project components. The stockroom was transformed from a labyrinth into a model of logical organization. Finding a 3mm Allen wrench went from a treasure hunt to a 5-second task.
c) Shine (Seiso): Cleanliness isn’t just about aesthetics; it’s about function. We established daily cleaning routines and more importantly, protocols for immediate cleanup of spills or messes. The shop floor started to look less like a workshop and more like a high-tech laboratory.
d) Standardize (Seiketsu): This step was crucial for sustainability. We developed clear, visual standards for workplace organization. Checklists, audit procedures, and standardized work instructions became the new normal. The key was making these standards visual and intuitive – no one reads a 50-page manual, but everyone understands a well-designed infographic.
e) Sustain (Shitsuke): This is where most 5S initiatives live or die. The company tackled it head-on by integrating 5S into their performance reviews, creating a peer auditing system, and even tying bonuses to 5S compliance. They made it clear that this wasn’t a flavor-of-the-month initiative; it was the new way of working.
Challenges: The Resistance
Obviously, it wasn’t all smooth sailing. Some veteran engineers viewed 5S as a threat to their free will. “I know where everything is in my mess,” was a common conversation. One other headache was Resource allocation, the process of implementing 5S took time away from projects, causing short-term pain.
The biggest unexpected obstacle was Information overload. In their enthusiasm, The company initially went overboard with documentation, creating a administrative nightmare that threatened to undo their progress.
Solutions: Adapt and Overcome
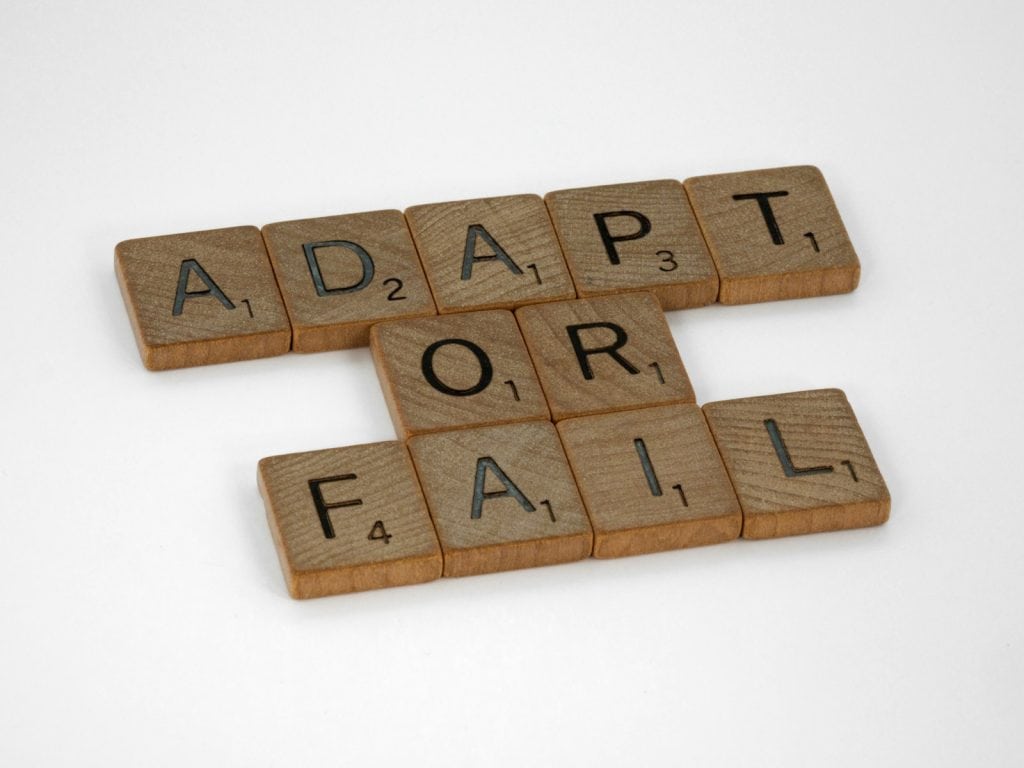
To combat resistance, the company got creative. They organized a “5S Challenge” competition between departments. By turning it into a competition it appealed to the engineers’ competitive nature. To resolve the issue around resource allocation, they gradually ramped up 5S activities, starting with pilot areas before full implementation.
To tackle the documentation overload, they brought in UX designers to streamline their visual management systems. The result was a set of intuitive, at-a-glance guides that conveyed critical information without the need for War and Peace-length manuals.
Results the Payoff
After 12 months, the results were nothing short of spectacular:
- Project completion times dropped by 35%, exceeding their target
- Quality defects plummeted by 11%
- Employee productivity surged by 25%
- Workplace injuries decreased by 45% (an unexpected bonus)
The before-and-after photos are some of my favourite. Gone were the cluttered workbenches and mystifying stockrooms. In their place stood a model of industrial efficiency, with every tool and component in its designated spot.
But the numbers only tell half the story. The real transformation was in the company culture. Employees who were initially skeptical became 5S evangelists. The pride in their workspace was incredible.
Lesson Learnt: The Wisdom Of Hindsight
The companys journey offered several key takeaways:
- Leadership buy-in is non-negotiable. The CEO needs to be as committed to 5S as the janitor.
- Training is an investment, not an expense. Skimp on education, and you’ll pay for it tenfold in poor execution.
- Adapt 5S to your culture, not vice versa. The company’s approach worked because it resonated with their engineers’ mindset.
- Sustainability requires accountability. Without clear metrics and consequences, 5S becomes just another corporate buzzword.
- Visual management is king. In a fast-paced environment, visual cues trump lengthy procedures every time.
- Future Plans: The Road Ahead
Since the initial project Company they haven’t slowed down. They’re exploring ways to apply 5S principles to their digital workspace, tackling the often-overlooked issue of digital clutter. They’re also investigating how AI and IoT can enhance their 5S system, potentially creating a self-auditing workspace.
The company is now eyeing a full lean transformation, with plans to implement kanban systems and value stream mapping across their operations. 5S was just the beginning of their lean journey, but it laid a rock-solid foundation for future improvements.
In conclusion, This 5S implementation wasn’t just about cleaning up their workspace; it was about fundamentally changing how they approached their work. It’s a testament to the power of lean principles when applied with intelligence and commitment.
As I often tell my clients, 5S isn’t about creating a pretty workspace. It’s about creating an environment where excellence is the only option. They didn’t just clean up their act; they set a new standard for operational excellence in their industry. And in today’s cut-throat market, that’s not just good business – it’s survival.